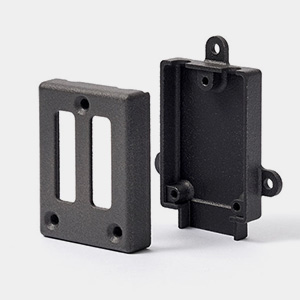
As the 3D printing industry has expanded over the years, new innovations have made many more options and opportunities available especially during the past decade. Our team at Shapeways is experienced in advising designers and engineers in the use of different hardware, software, and materials for both business and industrial use.
In this article, we’re focusing on one specific technology called Selective Laser Sintering (SLS), which is the original form of 3D printing created back in the 80s, as a particularly good choice for products that require high quality and high accuracy.
Materials printed in SLS include Nylon 11 (also known as SLS PA11, EOS PA11, Nylon Polyamide 11), Nylon 12 (also known as Nylon 12 Plastic, PA12, Polyamide, PA 2200), and Thermoplastic Polyurethane (TPU).
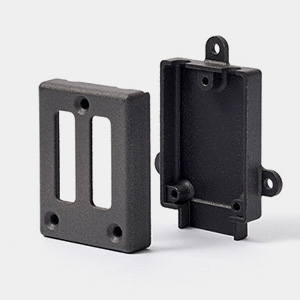
Rather than extruding plastic filament to be deposited layer by layer onto a platform like a glass print bed (as in the more affordable and consumer-driven FDM 3D printing), SLS 3D printers rely on effective laser technology that fuses particles of powder together to create your desired object—usually white or monotone in color, although dying is also an option for select materials in the finishing process, along with sanding and smoothing.
SLS 3D printing offers benefits such as greater strength and predictability in material and mechanical properties, no need for supports due to the bolstering of the powder, and the ability to design and produce complex geometries. Some spectacular and inspiring application examples include the following:
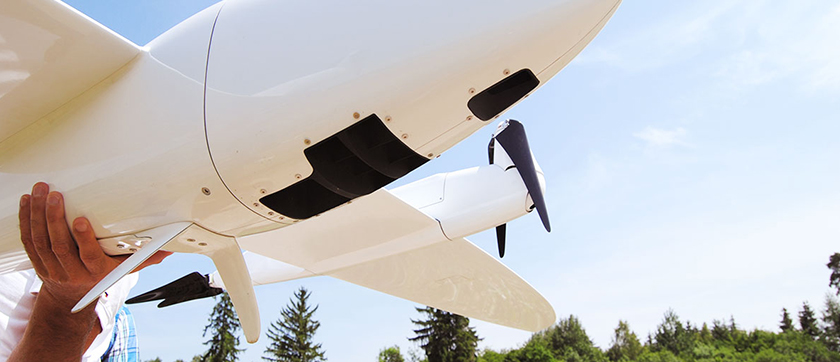
Additive manufacturing and its versatility from design to production is hugely appealing to many aerospace engineers. When parts are printed in Nylon materials using SLS technology, engineers expect these parts to be durable for flight and space travel, as well as lightweight and flame retardant. Parts can be manufactured on demand—even if only one part is needed—to create exterior or interiors aircraft parts, satellites, antennas, or drones.
- Automotive – automotive manufacturing are using AM processes today for critical prototyping as well as high-performance parts. In addition, the ability to fabricate obsolete components is another great benefit of AM technology that auto shops around the world are utilizing.
For example, an automotive engineer may be working on a vintage car in need of replacement for a small, detailed luxury feature that is out of stock, or a railway company may need to replace a part that has been in use for decades but is no longer in production.
With modern technology, the ability to 3D scan an item and 3D print one or many of the part in need, this has completely changed the landscape for spare parts management, making the production of previously-unavailable parts fast, easy, and much more affordable.
- Mechanical – Shapeways can 3D print parts on both small and large scales with SLS 3D printing, whether you are looking for detailed hinges or gaskets and seals for an air vent. While these types of objects can prove difficult to produce via digital fabrication, using an SLS printer will allow you to achieve precision and high-dimensional accuracy to ensure the perfect fit.
- Medical devices – 3D printed medical models and a variety of different implants have already dramatically improved patient-specific treatment including custom prosthetics and orthotics, and there’s great potential for advanced developments such as the fabrication of human organs to be more widely available in the near future.

Lightweight yet strong devices can be fabricated much more affordably and in a fraction of the time when compared to conventional techniques for devices like hand splints. The improved process for creating these devices are further appreciated to meet the needs of young patients who will need frequent replacements as they grow.
- Footwear and insoles – While 3D printing has been responsible for a notable impact on the footwear industry (from ergonomic flats to high-end running shoes), thermoplastics allow for patient-specific insoles to be created, presenting better support and improved comfort for patients. Again, speed in production is an important benefit, along with longevity of quality benefits.
Try Nylon 11, in natural white finish, for exterior biomedical applications as well as auto parts, mechanical parts, sports equipment, and components where high tensile strength, durability, and impact resistance are required.
Nylon 12 is commonly chosen for many different prototypes and functional products such as hinges, springs, cases, prosthetics, and different types of parts requiring strength and stiffness or interlocking parts. Our Premium finish is also available for an even higher quality texture and look. Colors (aside from the default natural white, and attained through dying) are also available in black, pink, red, orange, yellow, green, blue, and purple. You may even choose to customize parts yourself in terms of finishing and coloring.
Thermoplastic Polyurethane—known for its rubbery texture, durability, and impact-resistance—is also used in medical and automotive applications, sports equipment, footwear, and items like hoses and seals. This material is available in off-white and is commonly used for end-use industrial products requiring some degree of elasticity.
Getting your products printed in SLS through Shapeways allows you to reap the rewards of manufacturing high-performance parts using quality materials without having to invest in hardware, software, and materials required for your build. Our company has worked with over a million users to help 3D printed over ten million products in 75+ different materials and finishes.
Enjoy the benefits of our advanced technology and wide range of materials for printing your creations with accuracy, complex detail, with no minimum or limits in terms of mass customization or single part orders. To find out more about how we can help with your project, get in touch with us now.
