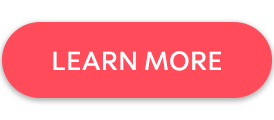
If practice makes perfect, then prototyping should lead to the perfect final product. But how does your business select the best-fit technology to prototype?
Dozens of options are available to choose
among when making a prototype. We’re going to explore why businesses are
choosing 3D printing for their prototypes.
Prototyping
From Concept To Creation
Prototyping typically involves a number of
stages, each requiring a physical product made to meet the needs of a
go-to-market step of a new design and subject to an array of testing
procedures.
These, broadly, include:
- Concept
- Assembly / Fit
- Functional
- Life Test
- Regulatory
From a rough conceptual creation that prioritizes speed and appearance, a prototype is necessary to bring a design from idea to the physical. The earliest stages of prototyping often require the fastest turnaround in fabrication, as getting an actual object in hand is the only way to gauge viability for product development.
As each stage of prototyping progresses,
though, needs change. The prototypes must become less rough around the edges as
those edges will be subject to testing for fit, functionality, mechanical
properties, and other physical needs.
A final prototype may often be visually if not
tactilely indistinguishable from an end-use product, which can help in showing
potential investors or creating marketing materials for a new product even
before mass production ramps up.
Speeding
Time-To-Market With Rapid Prototyping
3D printing is a young technology suite, and
one with many names. While it is increasingly referred to as additive
manufacturing today, with end-use part production possible, most notably for
low-volume or spare parts manufacture, the technology’s first nomenclature in
the 1980s was synonymous with its initial primary use: rapid prototyping.
When you speak to someone who’s been in this
industry since its early days, they may still naturally refer to “rapid
prototyping” or “RP” more often than “3D printing” or “additive manufacturing”
through many years of ingrained habit.
Decades later, rapid prototyping remains the
primary application for 3D printing technologies across the world.
What is it about 3D printing that adds the
“rapid” to “prototyping”? Digitization.
Taking a 3D model directly to a 3D printer for
fabrication speeds the process of prototyping. Digital models can be made quite
quickly using a variety of 3D printing technologies, removing the needs for
many steps in other, more traditional fabrication technologies. No tooling is
needed, for example, nor is there a waiting period while molds are made and
filled. It’s also much faster and more precise than hand-fabricating.
Additive manufacturing adds material, rather
than removing it from blocks as is done in subtractive methods like CNC, saving
on costs of materials that even for prototypes can run up total project costs.
3D
Printing Process & Materials For Prototyping
The selection of 3D printing process and
material can be adjusted for specific needs at every stage of product design.
During initial prototyping stages, a low-cost
material can be used with low infill and thicker layers, lowering material
costs and speeding print time to create a rough-and-ready first look at a new
design.
Whether plastic or metal, 3D printing can
quickly fabricate a product that will come to look and feel just like the
desired end result.
By starting with a low-cost plastic material
and moving after a few iterations to metal, for example, a product that will
eventually be conventionally fabricated using metal can come to market much
more quickly than would be the case by machining each iteration — a
traditional pathway that ultimately costs much more in terms of time, money,
and labor.
Following early proof-of-concept stages,
subsequent versions can be made similarly quickly to get to just the right look
and fit before moving into more finessed prototypes. Tweaking a digital file to
adjust for better look, fit, appropriate scale, or other needs can be done
quickly, with a next iteration 3D printed potentially same-day.
Some 3D printing options, like HP and Carbon, also enable the capability of prototyping and producing on the same system or family, as different materials and parameters can move ever closer to a market-ready product. By iterating on the same system that will be used for the final product, quality control can be kept in-hand every step of the way, meaning there are no surprises when the first end-use production begins.
3D
Printing For Prototyping
When working with a service bureau like
Shapeways, additional expertise and access to different technology suites comes
into play for a high-quality experience every step of the way.
Shapeways’ rapid prototyping services offer:
Fast Turnaround
Our quick print turnaround times ensure that you’ll get your prototypes back faster than you would with traditional manufacturing processes.
Variety of Materials
Our wide selection of materials allows you to test your products in everything from plastic to metals.
Reliable Quality
Our high quality enables you to assess factors such as ergonomics, usability, manufacturability, and material testing.
When it’s time to move to the next phases of prototyping, a different 3D printing process and/or material may be in order to start getting into the right look and feel for a final product. Working with an experienced service partner offers helpful guidance in making these selections and moving on rapidly to the next iteration, ensuring the right choice is made at every step and keeping your project on track, on time, and looking just as you designed it.
