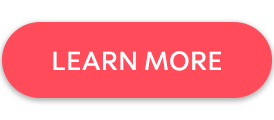
A building’s facade
is a challenging, multi-functional aspect of the structure that carries a lot
of responsibility and expectations. It acts as a barrier and protects the
inside from the elements, determines how much light enters the space and also
provides the overall aesthetic to the building. Find out how architects are
using 3D printing to streamline architectural design and construction
processes, freeing up more time and costs to continue innovating.
“Deep
Facade” from ETH Zurich Uses 3D Printing to Produce Complex Geometric Shapes
Deep Facade is a 6×4 meter aluminium structure composed of 26 sections of looping metal cast in a 3D printed open sand mold. It was created by students from the Digital Fabrication course at ETH Zurich in 2018 and evokes the folds of the cerebral cortex. This process makes use of the computational design method called topology optimization, where lightweight material can be used to create highly stable and efficient structures. They used binder jetting technology to fabricate the sand molds which allowed them substantial geometric freedom and sped up the fabrication process due to fast printing time, eliminating patternmaking and reducing material waste. The complexity of the geometric shapes of Deep Facade would not have been possible without the use of digital design and 3D printing. Each mold took under 12 hours to print and once printing began the facade itself was formed in less than half a week. The students’ work on Deep Facade demonstrated that the production of parts with 3D printed sand molds was faster and cheaper than traditional mold making methods, and also showed how efficiently one of a kind complex geometric designs could be produced.
FIT
Additive Manufacturing Group’s “Facade 3000” Demonstrates the Potential for
Mass Individualization with 3D Printing
In Lupburg Germany, FIT created a 3D printed aluminium facade for its boarding house made up of panels each with its own complex pattern of cavities to showcase how to use 3D printing in construction to favor economical individualization. The panels each have a unique arrangement of cavity shapes, each created using aluminium inserts in the molds. They were able to produce 20 different panels simultaneously in rotation. This method of producing unique panel pieces demonstrates that 3D printing is a key resource when it comes to the future of cost-effective mass-individualization and customization in construction.
1 South
First Building by COOKFOX Architects Finds Higher Productivity and Durability
with 3D Printed Molds
The new building at the site of the former Domino Sugar Factory in Brooklyn, NY. consists of two interlocking structures with facades of all-white concrete precast from 3D printed molds. The crystalline facades were designed to emulate sugar crystals and are self-shading with each piece shaped according to its solar orientation. The variations in the panels meant that over 100 different molds were needed, and creating each one took between 14-16 hours instead of taking 40-50 hours each if the molds were made traditionally. The efficiency of the molding process freed up substantial time and the 3D printed molds proved to be more durable than traditional wood and fiberglass molds (which can be used up to 10 times), as they were able to be reused 150-200 times.
Rainier
Square Tower in Seattle by 3Diligent Corp x Walters & Wolf Use 3D Printed
Parts for Better Accuracy and Reliability
In order to create an upward slope from the 4th to the 40th floor in the 59-story Rainier Square Tower in Seattle, Walters & Wolf and digital manufacturing company 3Diligent Corp printed aluminium nodes and wall curtains. 140 3D printed v-shaped nodes and square cut pieces of curtain wall were custom fabricated to geometrically accommodate a different angle for each section of the building. 3Diligent gave Walters & Wolf the option between investment casting and 3d printing and Walters & Wolf decided to use the 3D printed nodes because of their level of precision and structural integrity. Each node was created with varying dimensions up to a cubic foot, another testament to the efficiency and flexibility of 3d printing.
The
“Fluid Morphology” Project in Munich Make Use of Fast Prototyping to Develop
Functionally Integrated Facades
At the Technical University in Munich, Moritz Mungenast and Studio 3F began a project to create a 3D printed facade envelope that integrates ventilation, insulation and shading to become the new facade of the Deutsches Museum in 2020. The facade design is flowing and translucent, resembling Shapeways’ translucent material Accura 60. Studio 3F built a 1.6×2.8 meter section to test for a year to improve the design before making another polycarbonate prototype. The team was able to print 1:1 scale models and prototypes along the way with ease, meaning they were able to fully comprehend the viability of their design, determine production costs, communicate their ideas to their clients and continue developing what they hope to be a widely used facade technology that combines form and function.
In addition to these innovative projects, more and more architecture firms are utilizing 3D printing to achieve a higher level of freedom in design and as a way of making processes more time and cost efficient. 3D printed molds hold up better than traditional wood casts and have a higher range of possibility when it comes to complex geometric shapes. Because of the range of materials available, 3D printing also assures a level of structural reliability for the printing of end-use parts.
Shapeways can print with a variety of materials, including stainless steel, translucent and high strength plastics, and can help you get started with producing custom molds and parts.