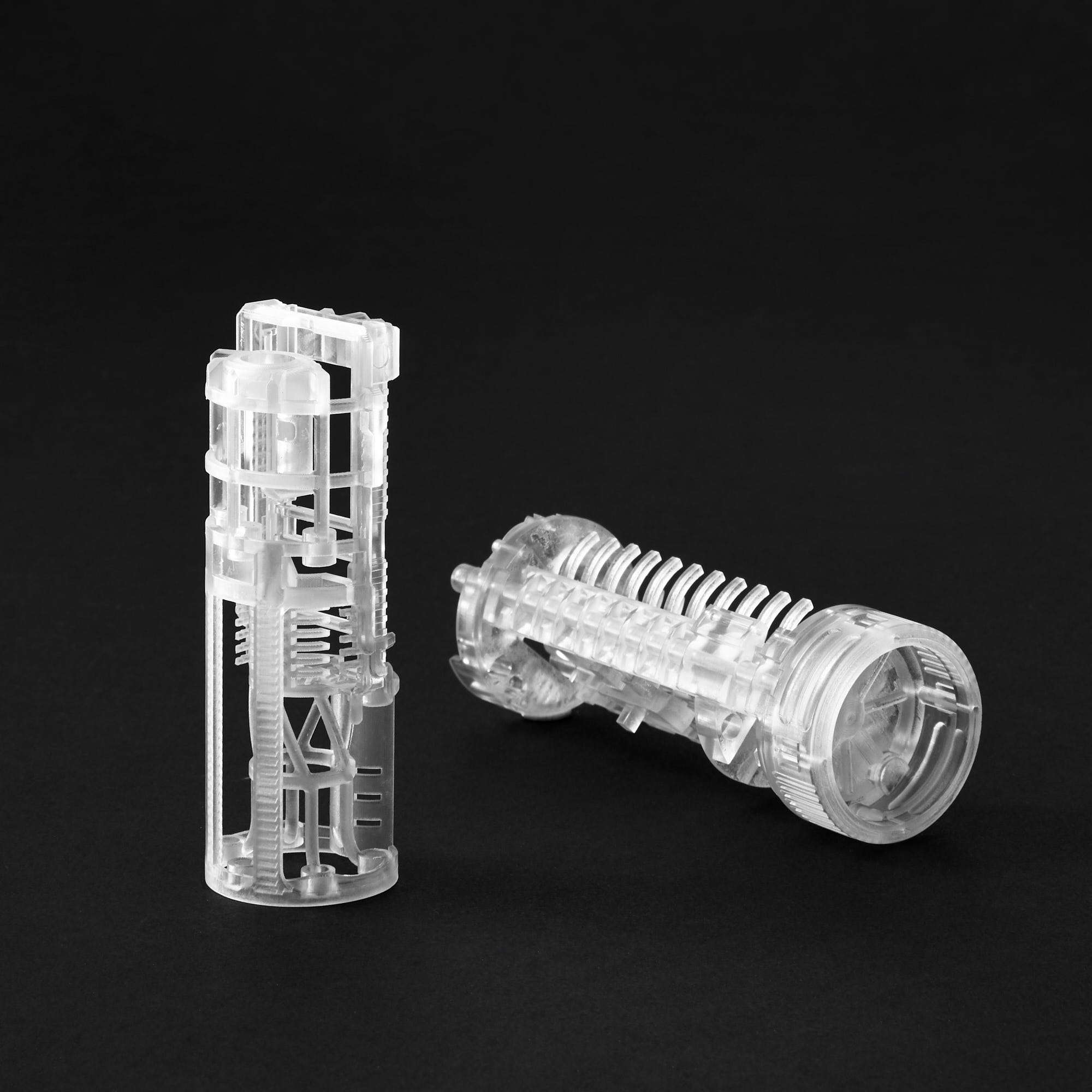
Innovation into infinity: that’s the beauty of 3D printing in a nutshell. Researchers, designers, engineers, and users working on so many different levels continue to break the mold whether in aerospace, automotive, electronics, or other applications – but with such a vast array of spectacular new projects comes new requirements too – and the need for different or better tools. As demand grows within the 3D printing industry for expanded options, and is met, users are given previously unheard-of latitude for digital fabrication every day.
When it comes to materials, unless you are a chemist, own a lab, or are recycling your own plastics into filament somehow, finding the right materials for producing parts or prototypes means working with experts like our team at Shapeways.
Currently we
offer materials to cover the needs of nearly any user engaged in the following
3D printing processes:
- Binder Jetting
- Digital Light Processing (DLP)
- Digital Light Synthesis (DLS)
- Material Jetting
- Multi Jet Fusion (MJF)
- Selective Laser Melting (SLM)
- Selective Laser Sintering (SLS)
- Stereolithography (SLA)
- Wax Casting
For this article, we’re going to focus on Stereolithography (SLA).
With the inception of SLA printing in the 80s (and a patent on the technology by Chuck Hull, who went on to found the illustrious 3D Systems), engineers were suddenly gifted with the magic of 3D printing via vat polymerization. A new industry slowly began to blossom as users enjoyed the wonders of rapid prototyping in critical applications, to include engineers and designers working for organizations like NASA and a handful of major automotive companies worldwide. As 3D printing continued to evolve and then explode into the mainstream over the last decade though, there has been some curiosity regarding the longevity of SLA – especially as so many other popular methods, namely FDM (Fused Deposition Modeling) 3D printing, have accelerated in popularity.
Stereolithography has stood the test of time despite greater access and affordability allowed by other processes. Requiring liquid resin, SLA relies on photopolymers to build models which are then cured by UV light, layer by layer. Users continue to be loyal to SLA over FDM 3D printing due to much greater accuracy in printing, and the ability to fabricate larger and more complex parts. FDM 3D printing is alluring to many due to a wider variety of choices in hardware and materials, along with the ability to produce large, simple parts – quickly. However, SLA 3D printing continues to shine as a better solution in many cases, such as when there is a need for printing jigs and molds with precision.
If you are
interested in uploading a design for 3D printing through Shapeways, the first
decision you need to make involves choosing one of our acrylate-based materials for
strength and accuracy in detail for your parts. When ordering SLA prints from
Shapeways, your options are as follows:
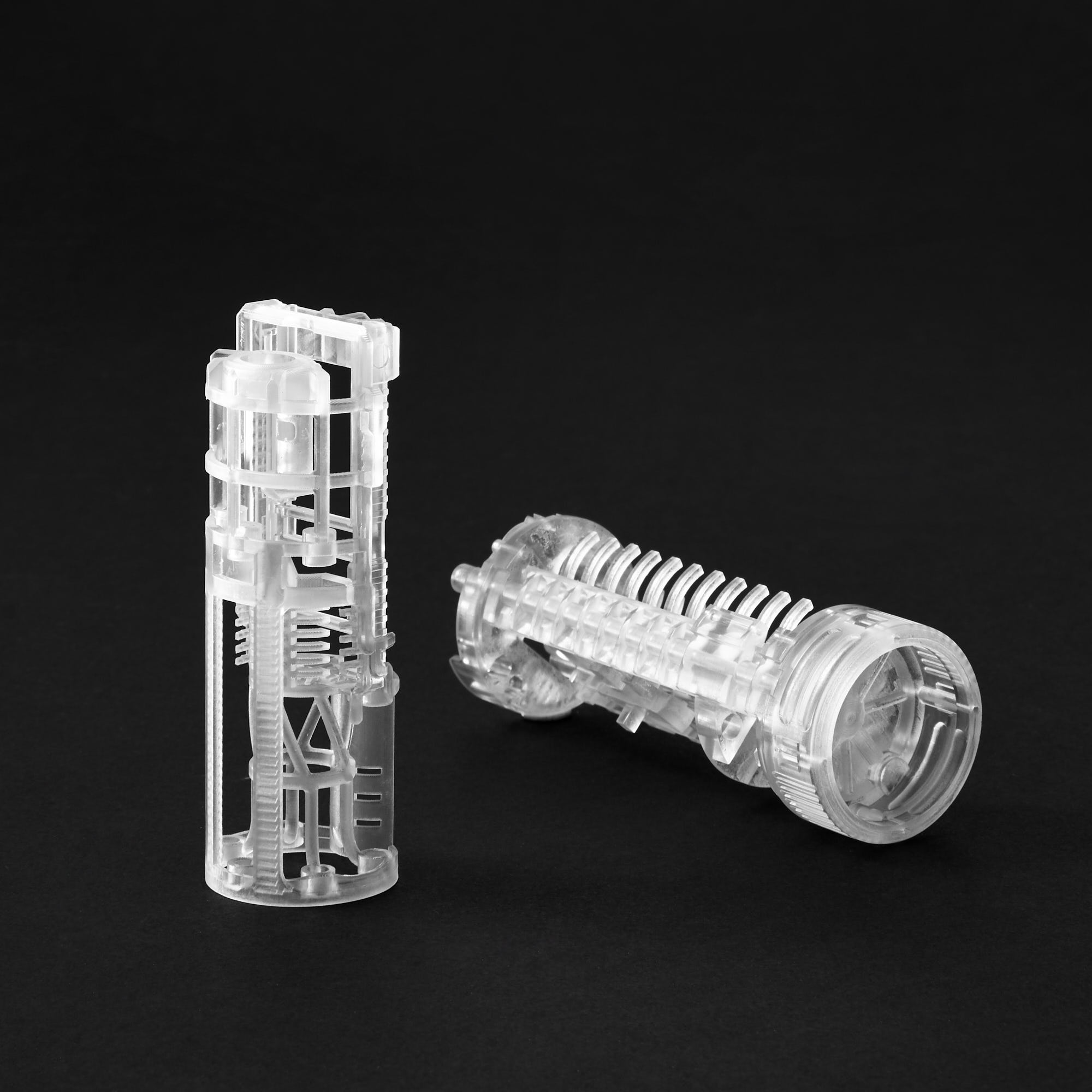
Accura® 60 – Semi-clear (with standard finishing) and rigid, this acrylate is suitable for 3D printing strong parts on the small to large scale, providing greater resolution, detail, smooth surfaces, and few layer lines. Similar to molded polycarbonate (PC), Accura 60 is also known as clear plastic, clear SLA, or translucent resin. We recommend this material for applications like functional lighting components, tech accessories, casting patterns, snap-fit assemblies, a wide range of prototypes, and clear, fluid flow visualization models. Accura 60 is watertight, with glass transition up to [TG] 58C/136F. For higher clarity, additional post-processing may be necessary.
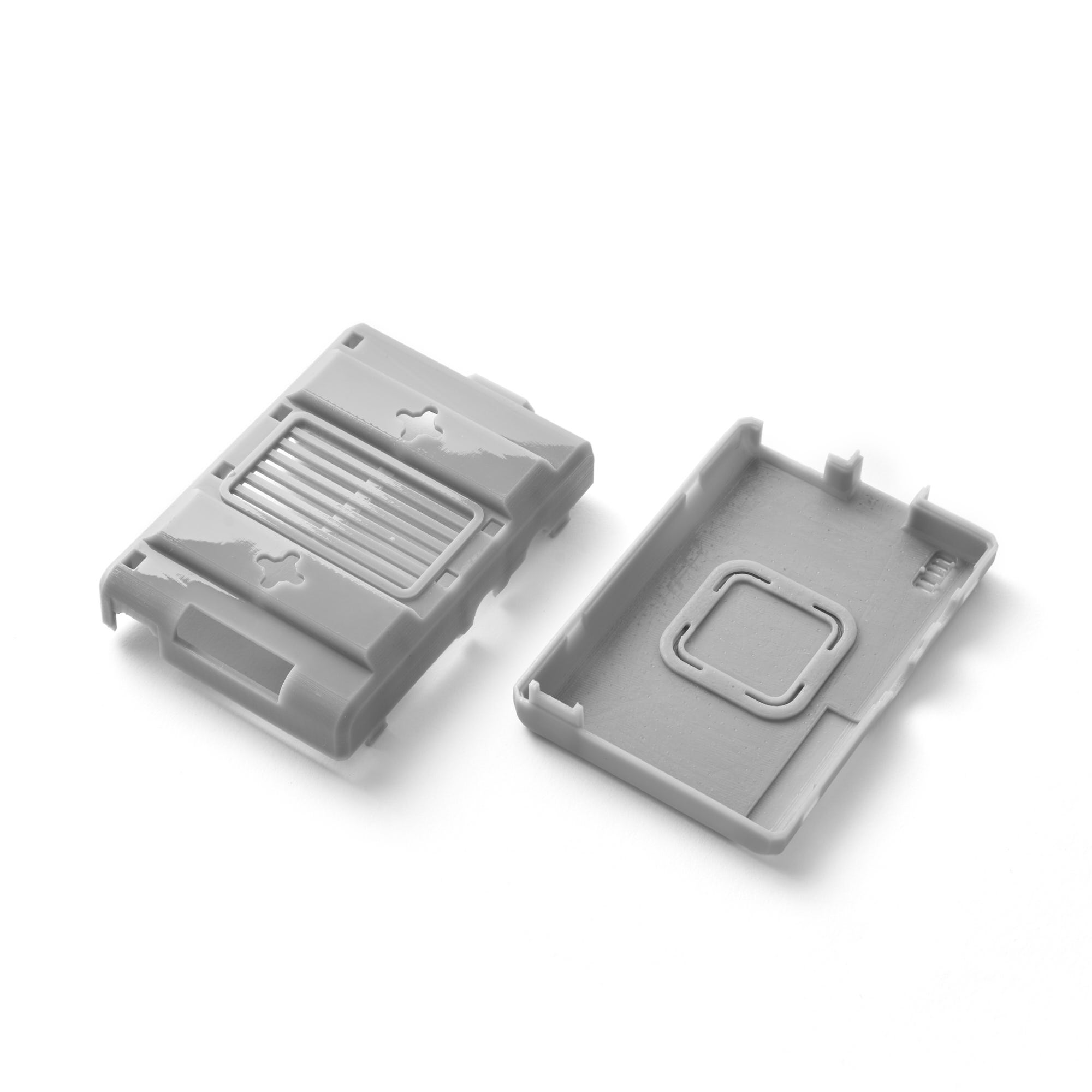
Accura® Xtreme™ – This gray plastic material is also meant for 3D printing a wide range of parts and prototypes from small to large, meant for fabrication of complex and functional assemblies featuring a smooth surface that is comparable to injection molding. Also known as Gray SLA or Gray Resin, Accura Xtreme is watertight, with glass transition up to [TG] 70C/158F. Recommended for 3D printing cases, models for displaying items, tech accessories, mechanical components, and snap-fit assemblies, Accura Xtreme is similar to other popular materials like Acrylonitrile Butadiene Styrene (ABS) or polypropylene. Standard finishing from Shapeways includes removal of supports and light sanding. This material offers fine detail, superior durability, along with moisture and temperature resistance.
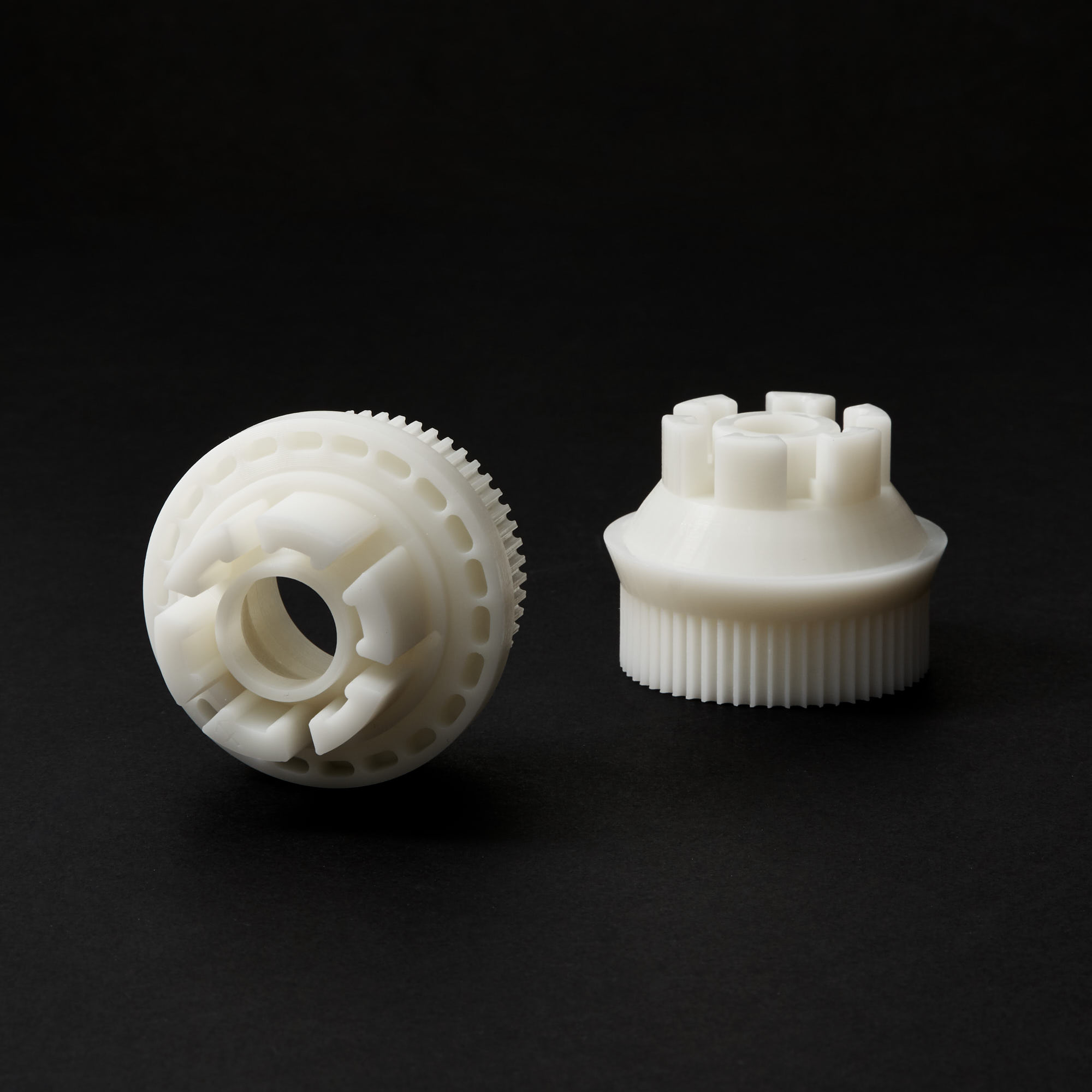
Accura® Xtreme™ White 200 – An ultra-tough white acrylate, this photopolymer resin offers good dimensional accuracy in parts, and excellence in strength, durability, and surface finish. Also known as White SLA, White Resin, or Accura Xtreme White 200, Accura Xtreme 200 is suited for fabrication of mechanical parts, display models, snap-fit assemblies, and master patterns for vacuum casting. This material is watertight, with glass transition up to [TG] 52C/126F. Standard finishing includes removal of supports and light sanding.
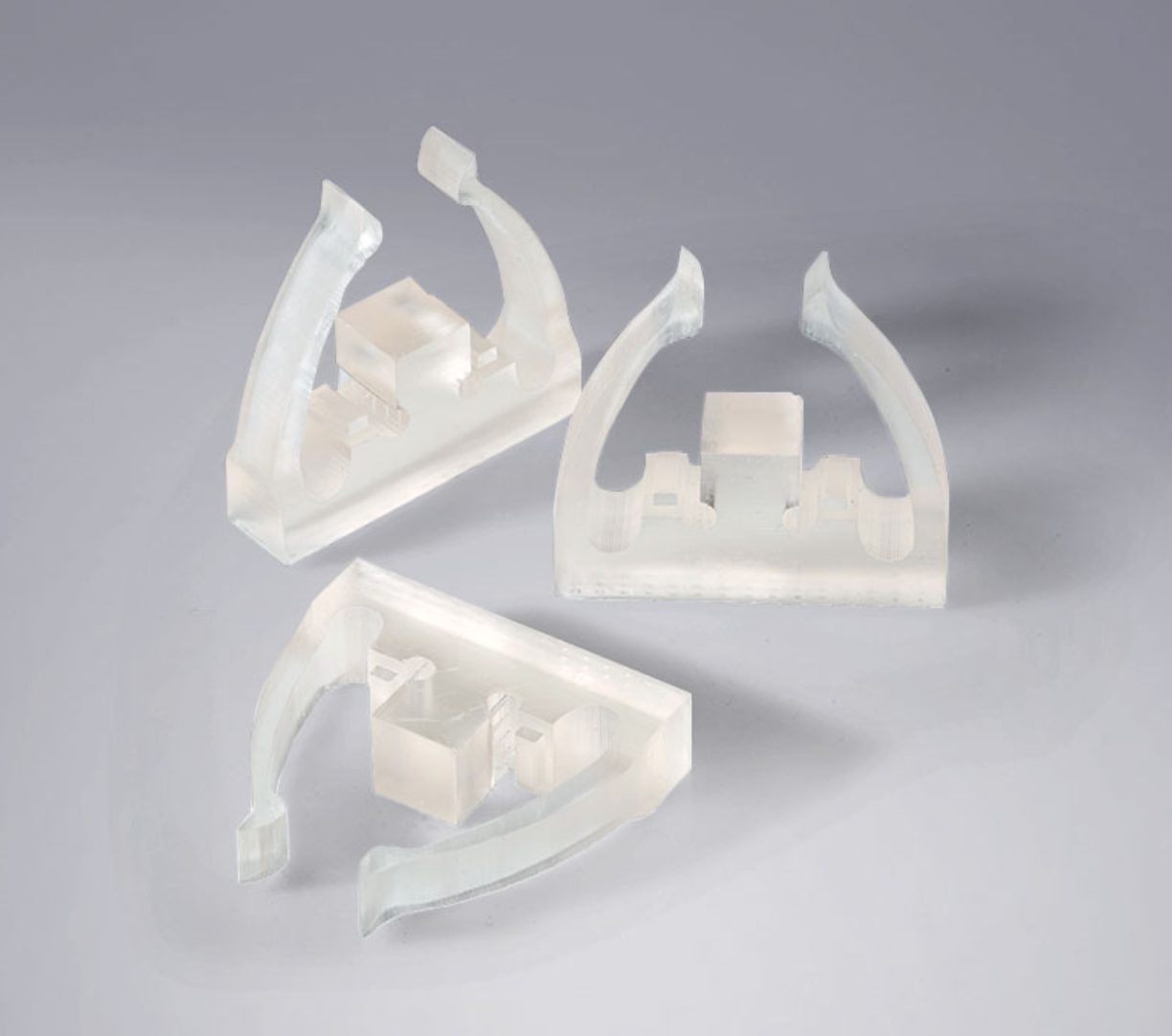
Ultracur3D® RG 35 – This Ultracur3D® rigid reactive urethane photopolymer is meant for 3D printing high-performance SLA (or DLP or LCD) parts. A resin used when superior resolution is required – along with excellence in surface quality and mechanical properties – RG 35 offers low shrinkage, and is recommended for fabrication of parts like jigs and fixtures, air ducts, sockets, and more.
Originally the number of materials may have been somewhat limited for SLA users, but we have continued to expand our offerings – especially as users have moved past using 3D printing as solely a prototyping tool and are relying on it to create functional parts, often for critical applications. 3D printing users have much higher expectations too as they make designs with greater complexity, requiring quality materials that promise higher performance and smoother surface finish.
Speak to a sales consultant at Shapeways if you have questions about how to develop your design or how to integrate 3D printed industrial products into your manufacturing program. We will continue to offer you the latest materials from forerunners in additive manufacturing – no matter what process you are engaged in – or what application you require parts and prototypes for.
Let our team will help you optimize designs, prototypes, and parts, providing comprehensive guidance from beginning to end.
