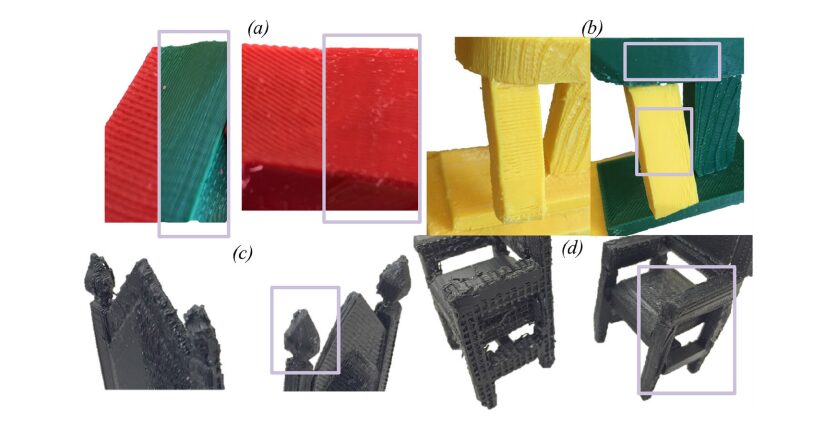
Les chercheurs İlke Demir, Daniel G. Aliaga et Bedrich Benes abordent l’un des sujets les plus populaires de l’impression 3D aujourd’hui: l’optimisation. Bien que les nombreux avantages de la fabrication numérique soient souvent discutés – d’une plus grande accessibilité, d’une vitesse de production améliorée et de la capacité de créer et de repenser sans intermédiaire – des défis continuent de se poser en raison de l’innovation continue. Toujours à la recherche de la perfection, les utilisateurs recherchent continuellement des moyens de prédire les propriétés mécaniques, de réduire les défauts et de surveiller les systèmes de fabrication additive.
Dans cette étude, les auteurs se concentrent sur la réduction de la quantité de matériau utilisé, la réduction des temps d’impression et le raffinement de la précision. Détaillant les efforts de leurs recherches dansDécomposition et superposition quasi convexes pour une impression 3D efficace», Nous en apprenons davantage sur leur« approche diviser pour mieux régner », qui comprend la décomposition et la configuration automatiques d’un objet d’entrée en composants prêts à imprimer.
«Les imprimantes 3D présentent à la fois des limites et des avantages en fonction de la cohérence entre les caractéristiques de l’imprimante et la géométrie du modèle», ont expliqué les auteurs. «Au lieu de compter uniquement sur les améliorations de la technologie d’impression 3D, nous proposons une solution qui optimise le modèle afin de maximiser cette cohérence en segmentant le modèle en composants facilement imprimables.»
Ils ont noté une amélioration de 15% de la qualité, une économie de 49,4% sur le matériel et une réduction de 50,3% de l’impression.

Décomposition pour l’impression 3D: modèle d’entrée (a), notre décomposition quasi convexe automatique (b), configuration qui sera imprimée (c), composants imprimés individuels (d) et objet imprimé et assemblé final (e).
L’échantillon de cette étude est un modèle polygonal. La décomposition comprenait la séparation des grappes de départ en un ensemble «optimal» de composants. À l’étape suivante, ils ont été préparés pour l’impression dans une phase de configuration, ce qui permet de gagner du temps car dans la plupart des autres cas, le travail est prolongé car le lit d’impression doit être abaissé ou la tête d’impression doit être déplacée vers le haut. La production est également plus efficace car les pièces sont imprimées en même temps. Lors de l’évaluation des propriétés, les chercheurs ont examiné:
- Approximation volumétrique
- Nombre de composants
- Quantité de matériel d’appui
- Temps d’impression plus rapide
- Haute qualité résultant de surfaces moins anguleuses

Pipeline système: un maillage 3D est d’abord décomposé en grappes puis optimisé pour des composants optimaux. Ensuite, les composants sont configurés pour une mise en page efficace. Enfin, imprimé et assemblé pour produire l’objet physique final.
L’algorithme consiste en la création et la segmentation de sous-espaces. Un ensemble de grappes de forme similaire (triangles) est défini, puis les grappes sont «fusionnées et divisées itérativement» pour l’équilibre.
«Au cours de chaque itération de cette étape, nous comparons cluster par cluster, marquons des clusters similaires et fusionnons à la fin de chaque itération, jusqu’à la convergence. Nous soulignons également que notre méthode utilise les mêmes valeurs de paramètres de seuil pour tous les modèles », expliquent les auteurs.
Pour une impression améliorée, les composants doivent posséder:
- Concavité
- Angles de surface
- Tailles et numéros
- Déviation
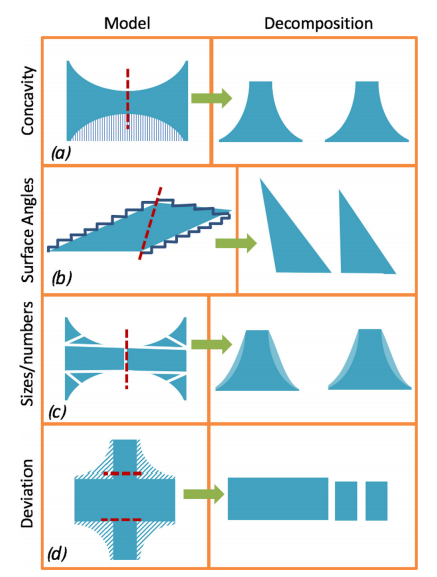
Propriétés des composants: les composants convexes nécessitent moins de matériau de support (a). Une meilleure qualité de surface peut être obtenue en évitant les angles presque horizontaux (b). Un équilibre entre la convexité et la taille / le nombre de composants empêche la sur-segmentation (c). La minimisation de l’écart augmente la fidélité du modèle (d). Les lignes pointillées rouges indiquent la ligne de coupe. La zone peignée en (a) indique la structure de support et les zones peignées en (c et d) indiquent l’écart du modèle.
Sur les 20 échantillons appliqués au cadre dans cette étude, certains ont été modélisés manuellement et certains ont été acquis commercialement. La complexité était en moyenne de 23,9 K, la nouvelle méthode convenant aux formes solides et à la coque. Le temps de prétraitement pour la segmentation et la configuration était d’environ 15 minutes pour un modèle de complexité moyenne.
Des exemples imprimés ont été comparés aux modèles initiaux et segmentés, «avec des surfaces mieux approchées et un support multicolore». Les modèles réels ont également été examinés dans leur forme initiale, après le retrait des supports, et avant et après l’assemblage.
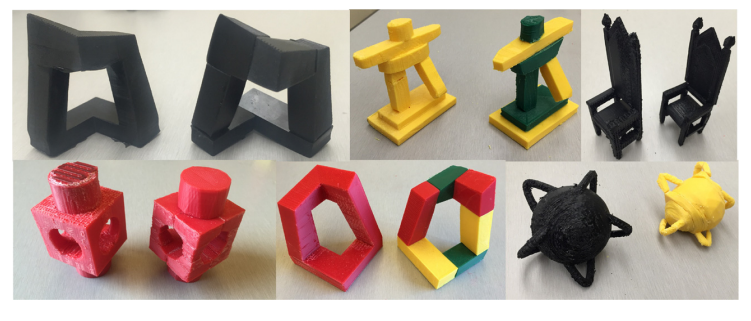
Exemples d’objets: Nous montrons côte à côte les résultats imprimés des modèles originaux et segmentés

Modèles originaux ou modèles segmentés: nous montrons les formes originales et segmentées du modèle, avant et après le post-traitement (en enlevant le matériau de support et l’assemblage, respectivement).
«… Notre approche évite le gaspillage de matériaux et fournit des objets de haute fidélité, avec un support multi-matériaux. Notez que, même si la surface approximative est très incurvée, notre décomposition trouve des segments qui se connectent bien, même après impression avec des erreurs d’impression accumulées. »
Les auteurs ont cependant noté que le modèle imprimé ne «rapprochait» pas l’original, bien que le modèle segmenté l’ait fait. En superposant les versions imprimées en filaire, ils ont pu montrer que de meilleures approximations pouvaient être obtenues en utilisant la même imprimante.
«La coloration dans la version nuage de points indique que notre algorithme a diminué l’erreur globale de plus de 35% en fonction de la distance de Hausdorff des points de surface échantillonnés. Nous n’avons pas évalué sur la base d’une mesure des modèles réels imprimés, car les paramètres contribuant à cette erreur de surface sont plus contraints en simulation », ont conclu les chercheurs.
«Nos résultats montrent que le cadre peut réduire le temps d’impression jusqu’à 65% (modélisation par dépôt fondu ou FDM) et 36% (stéréolithographie ou SLA) en moyenne et diminuer la consommation de matériau jusqu’à 35% (FDM) et 10% (SLA) sur les imprimantes grand public, tout en fournissant des objets plus précis. «

Évaluation: Comparaison des modèles originaux et segmentés, de leurs temps d’impression et de la consommation de matière, par modèle et par type d’imprimante.
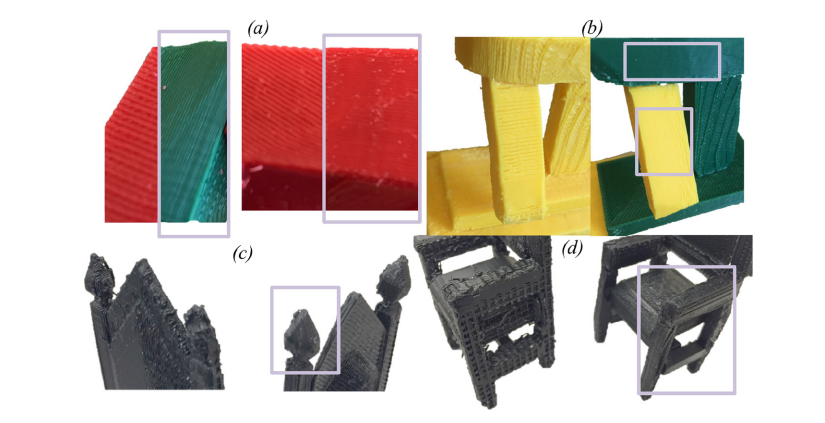
Améliorations: Nos résultats sont mis en évidence dans des encadrés. L’évitement des surfaces inclinées améliore la fidélité de la surface (a et b), l’absence de matériau de support protège la détérioration de l’objet (c), la convexité se débarrasse du matériau de support (et de ses cicatrices) de l’intérieur et de l’extérieur des objets (d ).
Que pensez-vous de cette nouvelle? Faites-nous part de vos pensées! Rejoignez la discussion sur ce sujet et d’autres sujets sur l’impression 3D sur 3DPrintBoard.com.
[Source/Images:‘[Source/Images:‘Décomposition et superposition quasi convexes pour une impression 3D efficace’]