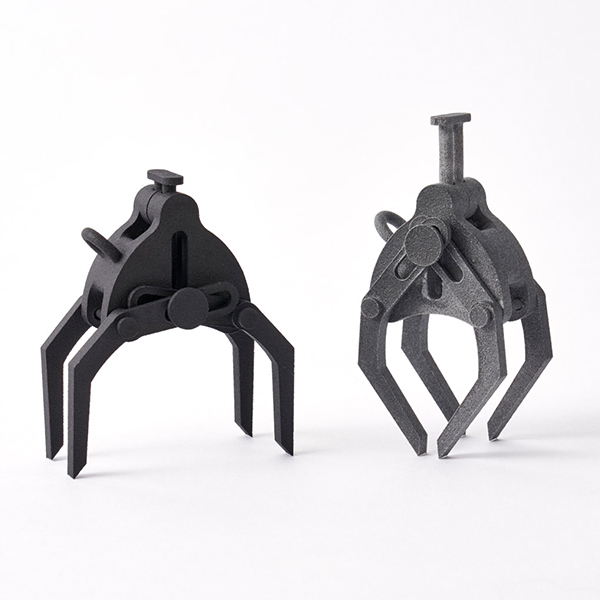
Opting to 3D print your prototype or functional part is a big step — but one that’s best served by selecting the best of the many 3D printing technologies available today. Shapeways offers more than 10 different 3D printing processes, with more than 90 material and finishing options available. Among these, a standout for making strong, durable, functional parts is Multi Jet Fusion (MJF) 3D printing. What exactly is this process, though, and when is it best put to use?
Understanding Multi Jet Fusion 3D Printing
MJF is a 3D printing process developed from HP Inc.’s longstanding expertise in inkjet technologies. This complex, powerful process uses powdered thermoplastic materials — like nylon 12 — to create detailed, dimensionally accurate parts with finely tuned mechanical properties.
The process itself entails a thin layer of
powdered material being deposited across the build platform. Droplets of fusing
and detailing agents are applied along with thermal energy on top of the
powdered material to define the part’s geometry. The precision of the inkjet
technology is such that builds can be controlled on a voxel level — that is,
at the 3D pixel level.
As a powder bed-based technology like SLS, MJF
3D printing can make parts without requiring support structures. This adds
additional design freedom as compared to other processes like SLA or FFF. Lack
of supports also allows for advanced design considerations like nesting to
increase build capacity, making this a great process for higher-volume
manufacturing. Following the 3D printing, the full powder bed unit is cooled
then loose powder is removed and recycled. Further finishing options can
include smoothing and dyeing to bring a naturally gray part to full vibrancy.
At Shapeways, available MJF materials
comprise:
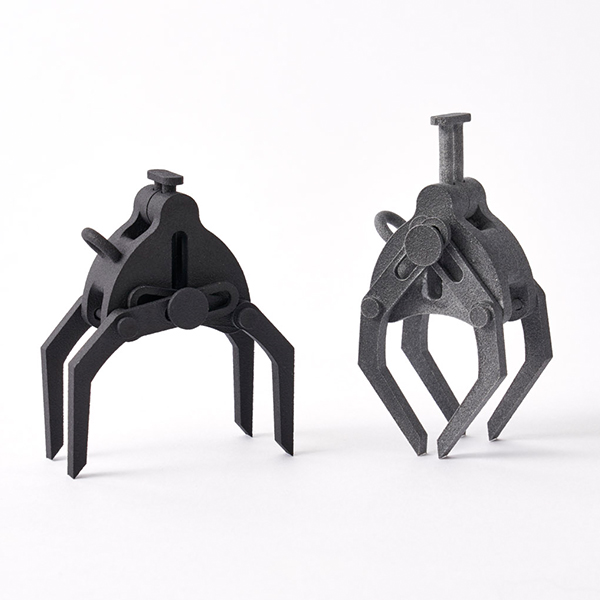
MJF PA12 – supports very complex geometries and thin features. HP’s nylon plastic offers excellent mechanical properties and a slightly grainy finish. In black, it is also available in a smooth and slightly glossy finish.
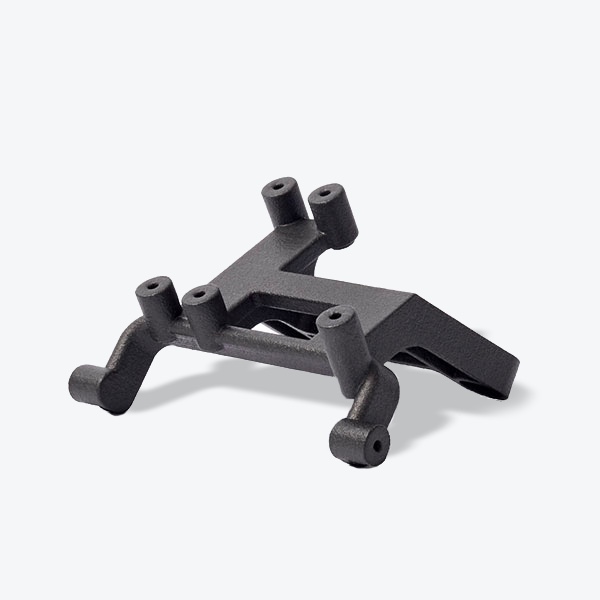
MJF Plastic PA12 Glass Beads – MJF nylon plastic infused with glass beads that improve product stiffness and structural integrity. This material is 40% glass-filled, which reduces warping during the 3D printing process and over the product’s life.
Multi Jet Fusion Applications
MJF is a great fit for building a strong,
durable part with fine detail and complex geometry. Larger-volume orders —
think economy of scale — are a breeze, as the speed and nesting capabilities
allow for production scale. Among some of the most popular uses for MJF 3D
printing are replacement parts, snap fits, living hinges, air-tight designs,
and end-use production. Applications can also be homed in by the choice of
material.
MJF Plastic PA12 is an ideal choice for a wide
range of applications from industrial parts to durable end-use goods. Its
strength, durability, and stiffness make it great for functional parts, such as
RC car parts and mounts. It is also popular for home decor, eyewear, and games.
PA12 Glass Beads is great for flat and large
parts that are prone to warping in Versatile Plastic and MJF PA12 Plastic, and
for functional parts that require high strength and dimensional accuracy.
Applications like robotics, drones, medical devices, housing and cases, and
tooling often benefit from use of this reinforced nylon material.
Multi Jet Fusion vs Selective Laser Sintering
Both MJF and SLS are powder bed 3D printing
options that can create complex geometries — but what’s the difference?
These processes have a lot in common, but each
also has its best-fit applications. In both SLS and MJF 3D printing, plastic
powder material is thermally fused layer-by-layer to build up the parts. SLS —
selective laser sintering — relies on a laser to sinter each point of a part,
while MJF’s fusing agent is dispensed via inkjet heads and fused using an
overhead infrared energy source. A detailing agent is also used, inhibiting
sintering of neighboring powder. In both processes, a finished 3D print job
must be fully cooled prior to excavating parts from the unsintered loose
powder. Actual print time is relatively comparable for both processes, though
MJF is faster to cool and post-process, while also maintaining a higher rate of
recoverable powder to be recycled.
The printheads used in the MJF process are
finer than an SLS laser spot size, enabling finer details and sharper edges.
For both processes, large, flat areas can be prone to warping.
Most SLS powders are white, allowing for easy
dyeing of finished parts. MJF parts, on the other hand, are naturally gray in
color. Shapeways’ finishing options include gray, black, and chemically
smoothed Smooth PA12, which is a slightly glossy black.
Both SLS and MJF 3D printing processes can
create strong, functional parts. The biggest differences lie in the precise
mechanical properties of a given 3D printing material, selected finishing
options, and the timing desired.
Multi Jet Fusion FAQ
What are
some design tips for MJF 3D printing?
- Material design guidelines for MJF PA12 and MJF PA12GB — and all other materials that Shapeways offers — are available here. Understanding the unique qualities of each material and potential finish ensures the right fit, such as designing interlocking or otherwise kinetic parts.
What qualities do MJF 3D printed materials offer?
- MJF PA12 Plastic is skin friendly, has a heat deflection of 95C/203F, watertight, and offers good chemical resistance.
- MJF PA12 Glass Beads Plastic has a heat deflection of 114C/247F, is skin-friendly, and offers good chemical resistance.
What colors and finishes are available from Shapeways for these materials?
- MJF PA12 Plastic:
- Gray: Medium gray with a matte and slightly grainy surface finish
- Black: Dyed black with a matte and slightly grainy surface finish.
- Black Smooth: Dyed black with a smooth and slightly glossy surface finish.
- MJF PA12 Glass Beads Plastic:
- Gray: Natural gray finish, blasted with oxide beads and air
- Dark Gray: Blasted with oxide beads and air, finished with a dark gray color
When MJF is the right 3D printing technology for your job, upload your 3D model to Shapeways for a quote to get the project started!
Sarah Goehrke is the founder of Additive Integrity, offering dedicated editorial services to the additive manufacturing industry. She is a regular contributor for Shapeways, on the Board of Directors of Women in 3D Printing, and the Managing Editor of Fabbaloo,