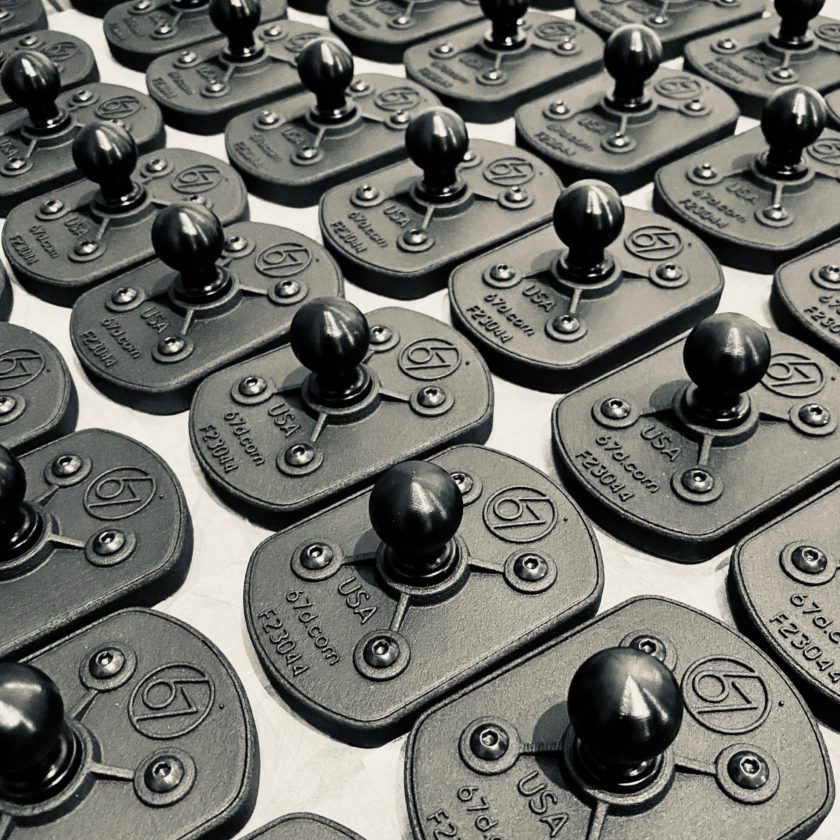
While this case study encompasses manufacturing for the MagMount, a new product that 67 Designs began working on recently, the real story began in 2012 as founder and CEO Gavin Stener decided to get back into design and engineering, opening a business to create high-end accessories for off-road vehicles.
With the trend for devices like tablets and iPads continuing
to tick upward, Stener noticed an obvious need for high-quality mounting
systems for tech-savvy users and their accompanying devices. Rather than
shooting for a consumer-driven pricepoint, however, the team at 67 designs was
more concerned with making an excellent and much needed design for drivers to
stow their tablets while driving (or even working at their desks).
“There’s only two types of quality,” explains Stener.
“There’s the quality of design, and then there’s the quality of conformance to
design—and you must have both of those.”
“Sometimes you can look at a product and it seems really
cool, but during the manufacturing process or due to the materials that have
been used, it doesn’t last very long. That perhaps is a sign that there wasn’t
good conformance to the design.”
Shapeways and 67 Designs were able to manufacture a third-generation product with the MagMount, and especially as the Shapeways team was able to clearly view the project as one driven by industrial business needs rather than that of an individual consumer. For Stener, an ongoing dedication to 3D printing meant sticking with use of the technology due to the intrinsic benefits available—despite more conventional ideology which might have pointed toward a return to traditional manufacturing in the face of success, and subsequent larger volumes.
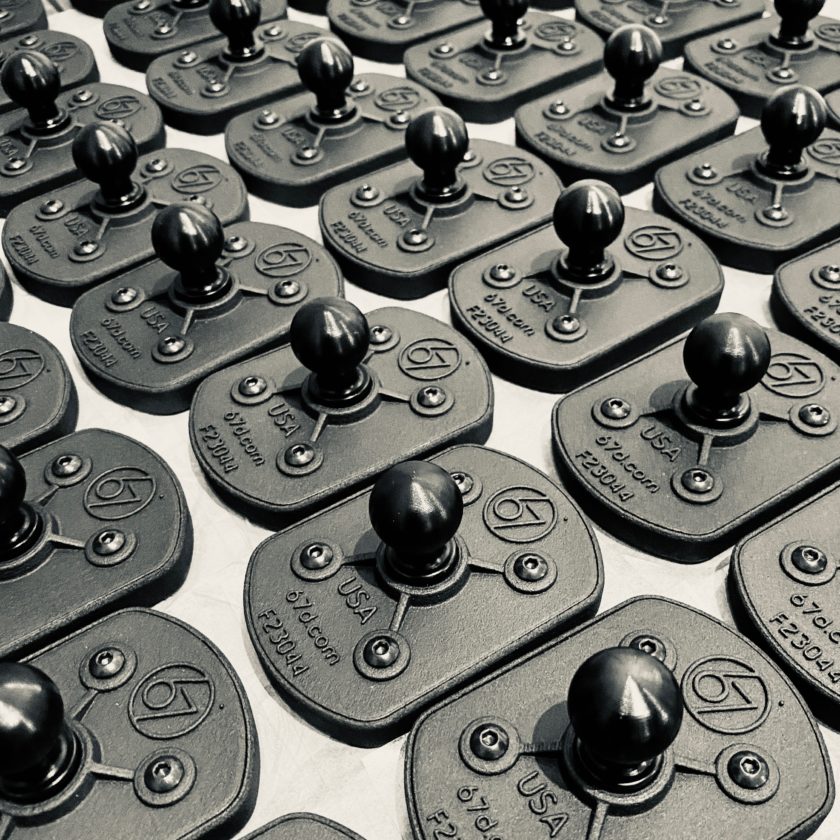
Selective laser sintering (SLS) offers tempting benefits for designers and especially with a material like Nylon 12. Used in a variety of applications—to include architecture, mechanical processes, prosthetics, environmental applications, and even luxury jewelry design, Stener settled on Nylon 12 for the MagMount due to the quality finish. 67 Designs devices are expected to be extremely rugged, so choice in materials is critical (especially considering the reputation the company has to uphold with so many rental vehicles using their products, and not one problem in five years).
Stener’s commitment to 67 Designs revolved around getting
back into industrial engineering, as well as a strong desire to be an active
member of his community:
“I made the decision to jump back to the industrial
engineering side, and a division of the company was originally meant to give
back and contribute to the community in which I live. Part of that was to have
fifty percent of the workforce made up of people with learning differences, and
the balance to be made up of experienced people in manufacturing.”
“It really started as a social mission.”
Stener is clearly fulfilling numerous, positive goals with 67 Designs as a vehicle. Enjoying a commitment to the promise of additive manufacturing, his company is producing quality products for adventurers around the world, living to the fullest (without leaving their technology behind). Workers are being hired and learning new skills, and Stener also allots time to focus on younger generations that may have little exposure to learning how to actually make things. The hope is that 3D printing will fill in some of those gaps, as well as teach students to take necessary risks in design and production.
For Stener, now responsible for a variety of successful high-quality offroading accessories, the rewards have obviously outweighed the risks.

Enjoy
the benefits of our advanced technology and wide range of materials for
printing your creations with accuracy, complex detail, and no minimum or limits
in terms of mass customization or single part orders. Read about case studies,
find out more about our solutions, and get instant quotes here.