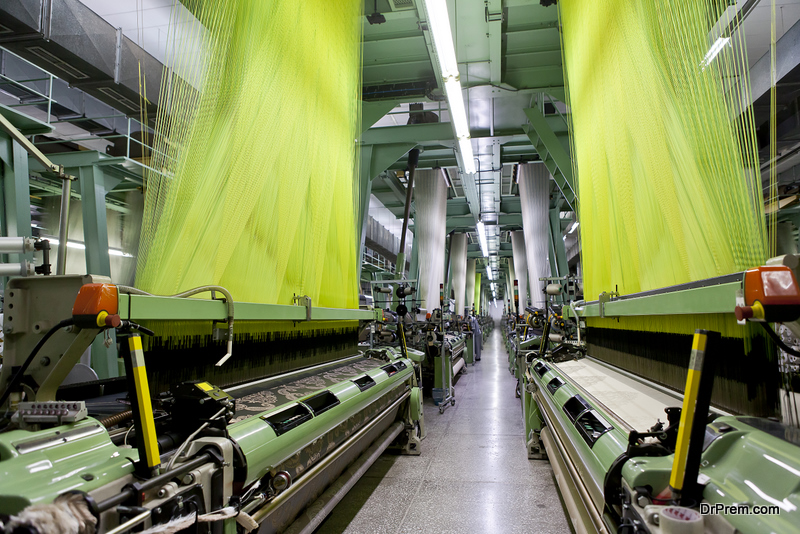
Little thought may be given to it, but each and every one of us is reliant on the textile industry. Be it fashionable or functional apparel, the industry is with us night and day, at work and at play. Although it is difficult to be exact, this global multi-billion-dollar industry employs around 430 million people. From processing and production, washing, dying, cutting, sewing and design, a multitude of skilled professionals, along with, a perhaps incalculable number, of manual labor personnel, have become reliant on the textile industry for their living.
The 430 million people reliant on the textile industry, representing 1 in 8 of the global workforce, is thought by many agencies to be a somewhat conservative estimate with the exact total perhaps being closer to 700 million. Whatever the exact total, the industry is massive, multi-faceted, and technologically advanced.
Since the dawn of man, covering the body has been a natural instinct. Initially man draped himself through practical necessity, but it wasn’t long before he combined this with beautification. This led further, and very soon a person’s apparel also became a symbol of status and power. Today, practicality, beautification and status still drive the direction of design, demand and production throughout the industry.
Ever increasing levels of demand for the supply of textiles led to the industry evolving and expanding into the fully automated goliath that it is today. Production en mass requires all manner of machinery to maintain production and consistent quality. Industrial fans are now vital, key components within the automated world of textile mass production.
Textile Production Process
The textile industry is now highly advanced engineers, chemists and computer programmers are as much to the industry as the humble weaver beavering away in their own cottage industry. With all the advancements and without going too deeply into the science of textile processing, there remains six basic steps to this age-old process.
Fiber Production
Textiles are made up of individual fibers which are arranged in a variety of different ways dependent on the required strength, durability, appearance of the final product. These fibers originate from four differing sources. Firstly, there are the plant fiber derivatives. These consist of cellulose and are commonly derived from cotton, linen, hemp or bamboo.
Then there are animal fibers which consist of proteins. The most common fibers within this group are wool and silk. Silk sourcing is very specific. The larva from the silk moth (Bombycidae) is the sole source making it an economically important insect. Wool, on the other hand, can be harvested from a variety of different animals as a source.
Lyocell and rayon, or viscose, are cellulosic man-made fibers that are usually sourced from wood pulp. Producing these fibers requires extensive chemical processing before they can proceed to the spinning process, which can be hazardous, and is very resource intensive.
Synthetic fibers are produced from the monomers drawn from fossil fuels. These monomers can then be bonded to form polymers, the polymer combinations that can be created are almost endless. For the most part, the majority of synthetic textiles are polyester, polyamide, aramide and polyacrylic. These products are also heavily reliant on potentially hazardous chemical processes.
Throughout the fiber production, fans play a vital role. Materials need to be moved in bulk and at a consistent pace, industrial fans make this possible. Fluids need to be pumped and sprayed, airborne toxins are removed and volume air spaces must be cleared of fibrous contaminants. These processes would not be possible without industrial fans.
Yarn Production
Following the production of the fibers, they then need to be spun. The age-old process of spinning with a spinning wheel is now entirely mechanical, automated and computer controlled. But this process also requires industrial fans. Not only to avail pneumatics to move the materials along the process, but also to bring oils to the yarn during the spinning. These oils reduce friction and increase the cohesion and strength of the fibers.
Fabric Production
The very essence of the textile industry is the production of fabric. Fabrics are either woven, non-woven or knitted. All of these processes require precise mechanical motion which is facilitated via pneumatics. It is industrial fans that supply a consistent, pressurized air flow that allows for the exactly repeating processes required for producing even quality fabrics.
It is during this process that the fibers are vulnerable to breakage. To maintain the strength of the yarn and to keep friction to a minimal level that chemicals and lubricants are also utilized in the process. Once again, it is industrial fans that deliver the fluids in the way required and to filter air where possible toxins or irritants may be expelled from the chemicals.
Pre-Treatments
These processes may be undertaken with the fibers, once the fibers have been spun into yarn or once the fabric has been produced. Pre-treatments add functional chemicals and prepare the materials for dying. The exact pre-treatments that are undertaken will depend on the type and blend of the fibers that make up the fabric.
There are 6 basic pre-treatments that are commonly undertaken. Washing is a generalized term used to describe the cleaning of a fabric after undergoing various steps or treatments during its processing. De-sizing is the removal of chemicals that remain in the warp yarns of the woven fabric.
Natural fibers will undergo scouring to remove waxes and grease which are prevalent within them whilst also removing any remaining cotton seeds and husks.
Bleaching makes the fibers whiter and facilitates the dyeing process. It also makes the fibers more absorbent. Carbonizing is a treatment process that removes and vegetable residue, such as seed pods. Cellulosic fibers will undergo mercerizing. Mercerizing causes the fibers to swell whilst also making them stronger and increasing their susceptibility to accept dying, this treatment will also increase the fabrics luster.
Dyeing and Printing
Dye components and the fixing chemicals are potentially hazardous, and thus tight controls are essential. Minimal human interaction with these processes is desirable, and with full automation this can be achieved. Industrial fans are essential in the movement of materials, fluids and air space control.
Although the use of textiles may have remained pretty much the same throughout man’s evolution, the types and the processes of creating them has evolved immeasurably. But this evolution would not have been possible, for both material production and worker safety, without axial and centrifugal industrial fans.
Article Submitted By Community Writer