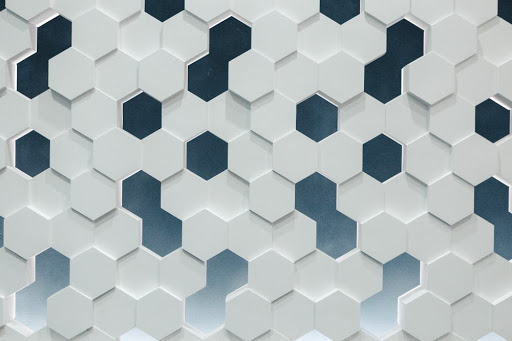
What would you picture if I told you to think about a strong manufacturing material? Chances are, some kind of metal comes to mind. Steel, iron, titanium — even their names inspire strength and durability.
And yet, ask anyone working on materials for high-performance applications what they’re placing their bets on, and you’ll probably hear buzz about carbon fiber, fiberglass, and other composite materials. So what’s the deal? Why did we start shifting away from a class of material that we’ve known about and mastered for millennia?
Clean Energy Trust’s latest investment in MITO Material Solutions is our answer to this question and our bet on the future of materials. But before we talk about MITO’s innovation, let’s dive into the world of composites.
What are Composite Materials?

Source: Wikimedia Commons
At the most basic level, composites consist of two materials that, when put together, are stronger than when separate. Typically, the combination involves a fiber-like reinforcement material and a glue-like matrix material.
Common real-world examples include steel reinforced concrete for highway bridges, where steel rebar acts as the reinforcement and concrete acts as the matrix, and plywood, where panels of wood planks or chips with alternating grain direction act as the reinforcement and glue acts as the matrix.

Steel rebar reinforcement on a bridge prior to adding concrete.
Source: Federal Highway Administration
The result of combining these materials to form composites typically involves a significant boost to strength and stiffness per unit of mass. In the highway bridge example, using either steel or concrete alone compromises on one of these two metrics.
Steel has high strength (meaning it doesn’t crack easily) but low stiffness (meaning it can deform with heavy loads), not to mention very heavy weight. Imagine making a bridge out of solid steel — setting aside the cost and difficulty of construction, the bridge would very quickly warp from the constant load of vehicles.
Concrete by itself has the opposite problem, with its low strength (notice those cracks on your driveway or sidewalk?) and high stiffness (try bending a piece of concrete). A solid concrete bridge would crumble quickly, especially in the winter when melting and refreezing ice expands surface cracks.
In today’s advanced manufacturing world, composite materials are primarily used to increase strength and/or reduce weight. Fiberglass and carbon fiber reinforced plastic are common examples here.
Fiberglass, or glass fiber reinforced plastic, is widely used in applications like home and building construction, wind turbine blades, and boats. It’s strong and stiff, and has an added bonus of fire resistance.
Carbon fiber reinforced plastic is more common in high-end and high-performance applications given the high cost of carbon fiber. Race cars and luxury consumer cars, professional mountain bikes, and golf clubs are just a few examples. Products and components made with carbon fiber are incredibly strong and lightweight — carbon fiber is twice as stiff as steel with one fifth the density.
As such, it’s no wonder that large manufacturing industries are already recognizing the benefits of composites and integrating them into production lines. For marine applications, composite materials used in boat construction are estimated to command a $1.5 billion market by 2024.
In the automotive sector, the market for exterior composite materials alone is projected to reach nearly $12 billion by 2024, and for under-the-hood component applications experts forecast a $6.7 billion market by 2023.
So What’s the Problem?
Though modern composite materials have been around for a while now, there’s a lot that still needs to be improved. As these materials are increasingly incorporated into high-performance applications, they face durability issues such as impact delamination, which causes materials to fracture into layers parallel to their surface. In critical components, this often translates into costly repairs or the use of heavy support structures.

Boat hull cross-section. Source: Wave to Wave Magazine
Take boats for example. Today, many types of commercial and recreational boats are built with fiberglass hulls. This fiberglass consists of layers of glass fiber cloth bonded together by resin, and has rapidly replaced aluminum and other hull construction materials over the years given its incredibly high strength to weight ratio. To further reduce weight and increase strength, most manufacturers also use a “wood core” construction, with a layer of wood sandwiched between exterior surfaces of fiberglass.
Severe delamination on a fiberglass hull. Source: A-1 Fiberglass Repairs
While this wood sandwich concept has been the product of years of manufacturing and engineering innovation, it’s not a perfect solution. Repeated pounding from waves and rocks can breach the surface of the fiberglass and allow water to seep into the resin matrix and wood core. Over time, the water can cause separation of the fiberglass and wood layers, wood rot, and delamination of the fiberglass itself to compromise the structural integrity of the hull. Left untreated, this can lead to tens of thousands of dollars in repairs (even more in larger boats) and affect the livelihoods of commercial fishermen and others who depend on their watercraft to make a living.
This type of delamination damage is common in not just boats, but in land-based vehicles as well. RVs, trailers, and heavy trucks that have fiberglass walls and sidings are just as susceptible.
Solutions in Progress
Delamination and other common failures of modern composites are not novel problems. Scientists and manufacturers have been working on engineering stronger and more durable composites for years.
One emerging approach has been to incorporate additive substances to the matrix material in composites in order to toughen it. Innovations in this space typically involve cutting edge materials such as graphene, nanosilica, and carbon nanotubes.

Model of a carbon nanotube. Source: Wikimedia Commons
Several of these novel materials have shown promise in adding durability but often come with significant drawbacks.
For example, graphene, nanosilica, and carbon nanotubes all tend to agglomerate into large chunks when mixed in with resins given their small particle size and large surface area. This significantly reduces the effectiveness of the additive as it decreases the surface area available to interface with the matrix and creates weak spots.
Furthermore, the particle sizes of these three substances are so small (nano-scale, to be precise) that they require specialized safety protocols for humans to work with them. Accidental inhalation can lead to severe respiratory and cardiovascular health issues as nano-scale particles are small enough to lodge into lung tissue at the cellular level. Talk about a bad cough.
Have No Fear, MITO is Here

MITO Material Solutions has developed a novel platform of composite-toughening additives featuring hybridized compounds of polyhedral oligomeric silsesquioxane (POSS). Quite a mouthful, right?
The gist of it is that MITO’s team has combined POSS, an existing additive, with other materials to produce a hybrid substance that can boost the performance of fiber reinforced composites by as much as 135%.
MITO’s E-GO product. Source: MITO Material Solutions
MITO’s first product, a hybrid of graphene oxide and epoxide POSS called “E-GO,” has been shown to offer these performance improvements at just a 0.1% concentration by weight.
Yeah, you read that right. This means that just two pounds of E-GO is enough to toughen a (literal) ton of composites. Beyond that, E-GO also features no agglomeration and micron-sized particles that are safe to handle.
So What?
Let’s go back to our very first question. Why are metals becoming increasingly obsolete in high-performance manufacturing?
We’ve already established that composite materials have a lot of potential in providing incredibly lightweight alternatives to metal; MITO’s products make this potential a reality.
With wide-ranging applications in industries such as long-haul trucking, sporting goods, marine transportation, and additive manufacturing, MITO has unlocked a new paradigm for manufacturing and a new world of possibilities in lightweight products.
Meet the MITOs

MITO wouldn’t be what it is today without the leadership and spunk of its founders, Haley and Kevin Keith.
A married power couple of entrepreneurs, Haley and Kevin took MITO out of the lab at Oklahoma State University and molded it into the promising business it is today.
Haley grew up in Elkhart, Indiana — the “RV Capital of the World” — and has been familiar with the concept of delamination since she was a kid.
After coming across an early version of what is now MITO’s core product through an MBA class at Oklahoma State, she immediately recognized its value and with the help of her husband Keith, a mechanical engineer, formed MITO Material Solutions.
At Clean Energy Trust, we pride ourselves in supporting some of the best and brightest entrepreneurs in the world. Haley and Kevin were no exceptions, and we are excited to add MITO to our portfolio and support the company in ushering in a new future of materials.
Read more of Clean Energy Trust’s news and perspectives on Medium.