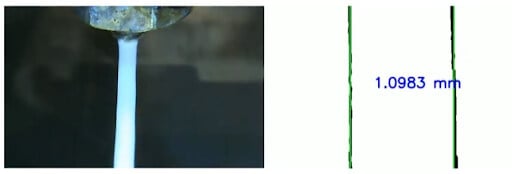
La surveillance in situ de l’état des matières premières est un sujet populaire parmi les chercheurs, quel que soit le type d’imprimante utilisé.
Des percées sont faites vers un meilleur contrôle de la qualité et une plus grande répétabilité grâce à l’utilisation de divers capteurs dans le processus d’impression à la fois sur métal et sur plastique, et ces technologies peuvent très bien se retrouver dans les produits de consommation… surtout s’il n’y a pas trop de matériel coûteux impliqué.
Une équipe de la Penn State University creuse une telle percée dans le domaine de l’impression FFF, et ils ont publié des détails sur leurs recherches sur la mesure des filaments assistée par vision par ordinateur dans la section Processus et systèmes de fabrication de la revue Materials.
À l’aide d’une caméra de microscope, d’une imprimante FFF et de tout un tas de codes, le chercheur Rakshith Badarinath s’est mis à utiliser la vision par ordinateur pour détecter la largeur (et donc le débit volumétrique) du filament extrudé lorsqu’il sortait de la buse chauffée. De plus, un thermocouple a été ajouté à la buse elle-même pour surveiller la température afin de déterminer tout impact que cela a également eu sur le filament extrudé. La température de sortie de la buse est essentielle pour déterminer la force de liaison intercouche (et la qualité de liaison) des pistes de filament déposées.
Au fur et à mesure que le filament est déposé, la caméra du microscope détecte les bords du filament avant d’appliquer un algorithme (appelé « algorithme de reconnaissance de largeur d’extrusion robuste (REXR) ») pour mesurer la largeur. À partir de la largeur, le volume peut être déterminé et, lorsqu’il est tracé en fonction du temps, un débit volumétrique est obtenu.
La mesure de la largeur d’extrusion s’est avérée être à moins de 0,08 mm des mesures de l’épaisseur et le débit déterminé s’est avéré suivre de près celui spécifié dans le logiciel de la trancheuse, ce qui signifie que les expériences ont démontré avec succès cette méthode de surveillance in situ des filaments.
Vidéo : mesure de la largeur d’extrusion basée sur la vision en temps réel
Contrôle de qualité
Les impressions défectueuses peuvent coûter du temps et des déchets, c’est pourquoi le développement de technologies de surveillance des processus est d’une importance vitale pour les industries qui souhaitent améliorer la qualité et la répétabilité tout en réduisant les coûts et les retouches.
La détection en temps réel des paramètres de processus clés améliore non seulement la qualité des matériaux extrudés, mais peut aider à mieux comprendre la physique du processus FFF, ce qui peut à son tour aider à construire de meilleurs modèles de prédiction. Un jour, nous verrons peut-être même des jumeaux numériques de processus d’impression, tous dotés de capteurs et d’algorithmes.
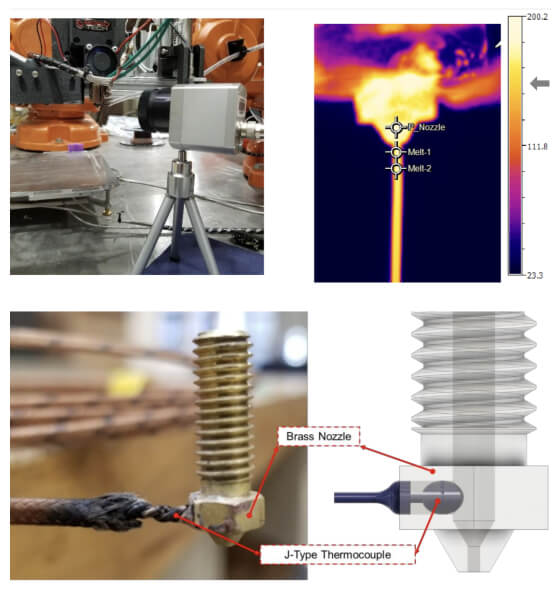
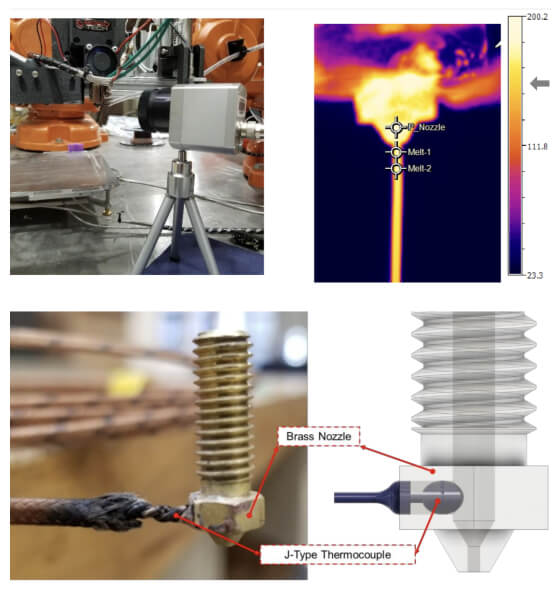
Vous pouvez voir la buse en laiton modifiée utilisée dans l’expérience dans l’image ci-dessus, ainsi que quelques images IR du filament sortant de la buse chaude. 2 types de filaments communs (PLA et PETG) ont été utilisés, et ils ont utilisé une imprimante de type bras robotisé.
Les chercheurs ont l’intention de continuer à développer le processus et déclarent que les améliorations des taux de mesure en temps réel du processus de dépôt doivent être améliorées avant que la technologie ne soit prête pour l’industrie.
Compte tenu de la démonstration du fonctionnement de la technologie, il ne semble pas exagéré de dire que nous verrons une forme de cette approche basée sur la vision de la détection de filament dans une imprimante près de chez vous dans un avenir pas trop lointain.
Vous pouvez lire l’article complet, intitulé « Détection en temps réel de la température d’écoulement du polymère de sortie et du débit volumétrique dans le processus de fabrication de filaments fondus » (accès gratuit), sur ce lien ici.
Histoire connexe