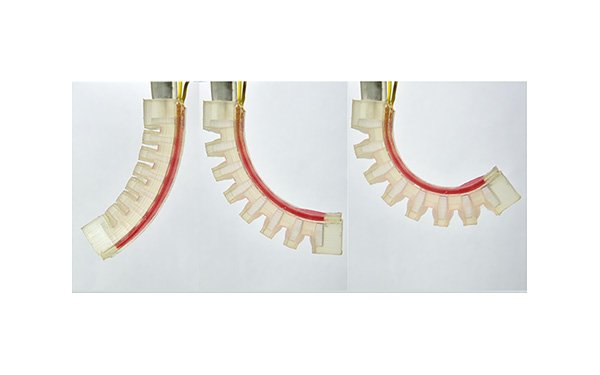
In 2018, we covered a research project where the team developed highly stretchable hydrogel for 3D printing that could be used in all sorts of applications, from bio-scaffolds for manufactured organs to flexible electronics. Now, that same team of researchers (plus some new members) from China, Singapore, and Israel have expanded on their previous work to include multi-material 3D printing of hydrogel and UV curable polymers.
Multi-material printing with hydrogel is possible, but the authors of the paper point out that “the current technologies constrain the geometries of hydrogel-polymer hybrids to laminates consisting of hydrogel with silicone rubbers,” which in turn “greatly limits functionality and performance of hydrogel-polymer-based devices and machines.” In other words, hydrogels can mostly be printed along with flexible silicone in geometries that are generally flat or consisting of few layers. The international team developed a method of printing high-water content acrylamide-PEGDA (AP) hydrogels with various UV curable resins in high-resolution 3D geometries where every material can be in the same layer.
Hydrogel-Polymer Hybrid 3D Printer
Of course, they had to build a custom DLP printer for their new method, and it’s a unique twist on the currently available technology. Rather than having the one large vat of a single material, they replaced it with a plate of glass that has concave cavities cut into the top face. Each of the cavities can hold a “puddle” of hydrogel or resin, and the glass plate moves horizontally in the printer to position the puddles between the UV projector and the printing platform that holds the printed object. When it’s time to print the hydrogel material, the glass plate slides the hydrogel puddle over the UV projector, the platform lowers the part-in-progress down to the bottom of the puddle, and the UV projector cures the layer with a short blast of light. The platform then lifts the part and the glass plate slides the resin puddle into position for its turn. It’s a fairly simple solution with a big payoff.
They print a number of fascinating objects to demonstrate what can be done, such as a Kelvin lattice made of hydrogel and a flexible elastomer. They also printed a three-material version of the same shape with a rigid polymer, hydrogel, and an elastomer, and it showed excellent stretching and unloading properties. The materials form “strong covalent bonds with the other two polymers, and we can stretch the hybrid Kelvin foam structure by large deformation without finding debonding between the unit cells printed with different materials,” meaning the materials bond together well.
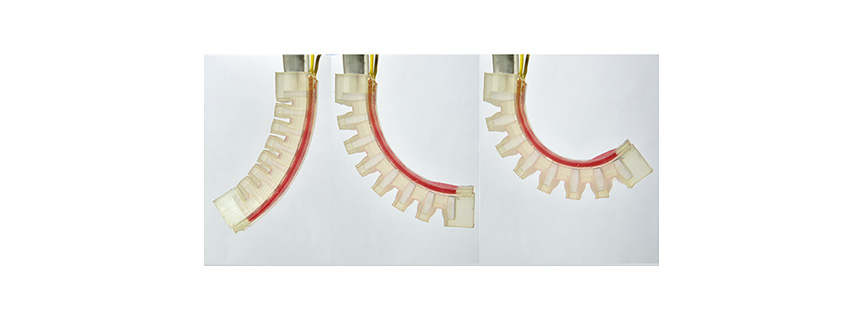
Soft pneumatic actuator. (Image credit: Science Advances )
Polymer-Reinforced Scaffolds and Strain-Sensing Actuators
Several rigid polymer-reinforced hydrogel composites were printed as well, where the rigid polymer was used to create a skeleton to reinforce the hydrogel shape. By affecting the density of the rigid lattice pattern, the stiffness of the entire object is affected, enabling soft-bodied objects with non-uniform stiffness.
Additionally, the team printed a soft pneumatic actuator with a conductive hydrogel strain sensor. A hydrogel strain-sensing circuit was integrated into a pneumatic actuator printed with an elastomer, and the device can detect the exact angle in which the actuator is positioned at any given moment by measuring the resistance (ohms) in the hydrogel circuit.
3D Printed Drug-Delivering Auto-Expanding Stent
Finally, they printed an SMP (shape memory polymer) vascular stent with a drug releasing function. The helical mesh-shaped stent was printed with a temperature-sensitive polymer and a hydrogel that’s loaded with “drugs.” After printing, the stent is “programmed” by compacting it into a narrow shape, which makes it easier to position into a blood vessel, and then storing it in a cold place. When the stent is warmed again upon entering a blood vessel, it returns to its original expanded shape, thus expanding the blood vessel. After the stent has expanded, the hydrogel begins to dissolve over 24 hours, delivering the drug in the process. That’s a lot of functionality packed into a 2mm stent.
It’s rare that researchers demonstrate so many real world applications with their laboratory breakthroughs, so this team deserves a round of applause for making functional prototypes of scaffolds, lattices, soft robotics and sensors, and drug-delivering stents that automatically expand.