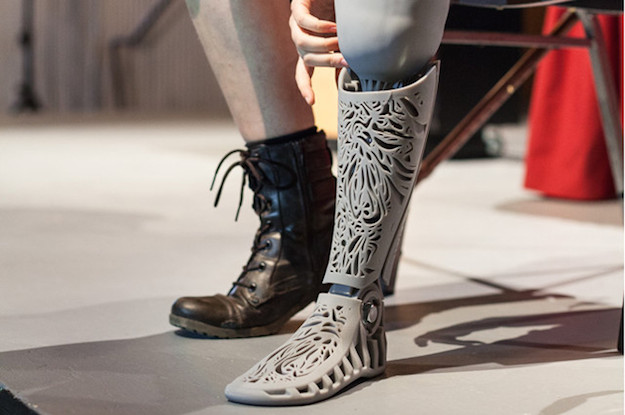
Although the incredibly versatile technology of 3D printing was invented for engineers to enjoy prototyping at rapid speed, it has expanded into so much more—driven by imagination—and fueled by specific needs in product development.
The
possibilities in medical applications are endless too, illustrating what is
undeniably now a critical aspect of 3D printing; after all, what could be more
important than improving the quality of human lives—or saving them?
One of the most
revered and most often discussed benefits of 3D printing is the ability to make
strong yet lightweight parts and prototypes that simply were not possible
before with conventional technology. This advantage is valuable to the medical
industry because the impacts are so positive, so immense, and only just
beginning.
The results of 3D printing are commonly so mind-boggling that the first descriptor brought to mind is “magical,” especially when considering the staggering potential in bioprinting. While the ultimate quest for so many researchers is in achieving the true 3D printing of human organs, there are already countless breakthroughs being made with 3D printed tissue—from the liver or kidney, as examples. Once that holy grail is reached it may not look anything like we once expected, but it is just a matter of time before highly functioning 3D printed organs are transplanted into human bodies.
In reality, there is no wizardry involved. Instead, it’s all about that perfect combination of advanced technology, advanced materials, innovation, and the tenacity required to make a difference. The secret to success lies in patient-specific treatment.
Medical models
The use of 3D
printed medical models is multi-layered, and enormously useful. Not only do
surgeons benefit by capturing a more detailed picture of rare conditions like
brain tumors, but there are extremely valuable educational uses for everyone
involved. While the doctor is able to diagnose and plot a course of treatment,
they are also able to use a detailed visual aid to explain to the patient what
is happening in the body, where, and how treatment and any possible surgery
will be performed.
The value for being able to rely on medical models rather than waiting for the availability of cadavers is extraordinary. Realistic, anatomically correct 3D printed models act as advanced training aids for medical students overall, but especially future surgeons. Experienced surgeons may also find themselves training with 3D printed models for weeks at a time as they prepare for rare or completely new procedures. This type of pre-planning means more streamlined procedures, less time in the operating room, and great advantage to the patient.
Materials used for medical models
MultiJet Fusion PA12 – Suitable for the creation of complex medical models, this versatile material is strong and durable—both important characteristics for parts that tend to be handled a lot over time.
Prosthetics, orthotics & exterior devices

3D printing has made an enormous impact in applications like prosthetics, orthotics, and exterior devices like knee braces. In prosthetics especially, quality of life can be improved for patients who may not have been able to afford limb replacements previously or did not want to wear them due to self-consciousness. For children and individuals of all ages in developing countries, the ability to offer extremely affordable prosthetics that can be made fast is life-changing. These devices can be completely customized to the wearer, offering unprecedented comfort—and in many cases, better options for style too that encourage the patient to actually use their prosthetics.
Orthotics can be made affordably and quickly with completely customized fit. As with prosthetics for children, the ability to 3D print new devices easily is a huge advantage in terms of growth spurts. This is also a huge departure from the past when some devices may have been fitted using conventional technology, with the child outgrowing prosthetics or orthotics before they were even delivered.
Materials used for prosthetics, orthotics & exterior devices
Nylon 11 – Offering high tensile strength, durability, and impact resistance, this nylon plastic is used to 3D print exterior medical devices like braces—used with selective laser sintering (SLS).
Nylon 12 [Versatile Plastic] – commonly used for prosthetics with (SLS) 3D printing, this nylon plastic is both strong and flexible, and lives up to its name in offering high-performance for a wide range of products.
MJF Plastic PA12 – Used with multi jet fusion technology, strong mechanical properties, durability, and stiffness make this nylon plastic popular for 3D printing prosthetics and other complex structures.
MJF Plastic PA12 Glass Beads – Used with MJF for medical braces, this 40 percent glass-filled material is suitable for parts requiring excellence in dimensional accuracy as well as strength.
Surgical guides and tools
The use of 3D printed surgical guides
and tools is again based around intensive customization, allowing for
patient-specific treatment. Today, a wide array of guides and tools can be
manufactured to streamline surgery, as well as dental procedures. The intent is
to give the surgeon a comprehensive plan to follow during any procedure,
whether performing hip replacements, knee replacements, dental surgeries, or
other operations.
3D printed surgical tools may include items like clamps and grasping devices, retractors, hemostats, and handles and other supporting features. The ability to customize these designs offers huge advantages to surgeons who may need to modify tools depending on procedures or their own preferences.
Materials used for surgical guides and tools
Nylon 12 [Versatile Plastic] – Used with SLS technology to 3D print strong 3D printed surgical guides and tools, this material is very popular in a wide range of applications due to its ability to be flexible for thinner parts while stiff for thicker parts and prototypes.
Stainless Steel 316L – Suitable for surgical tools, this industrial metal is corrosion-resistant and extremely strong, used with binder jetting technology.
Multi-color 3D printing for complex models
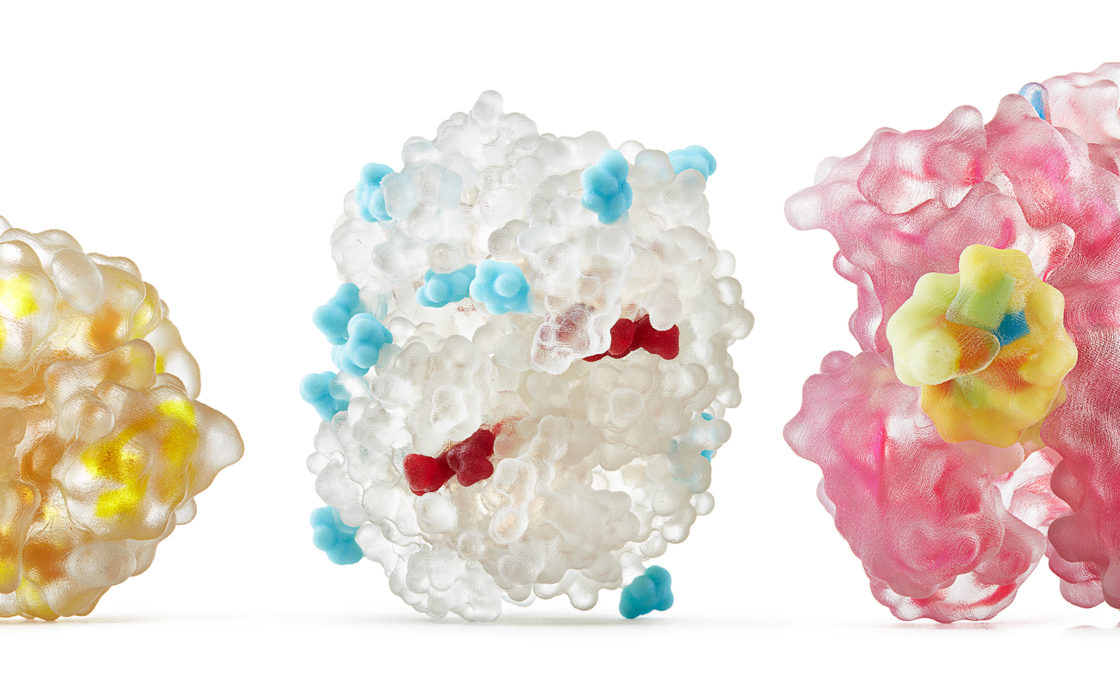
For several years now, Shapeways has offered full-color prints via the Stratasys J750 printer. Casey Steffen of Biologic Models, for example, relies on complex 3D printed protein models and 3D medical animations for his business.
Using
transparent plastic with the J750 allows for clear visualizations of the
“delicate internal protein structures” Steffen and his customers must examine.
3D printing in color is also an extremely valuable tool for color coding
models.
“With a color-coded model, an educator can easily explain how a
certain drug functions, the property of the protein, or how mutation changes
protein behavior by pointing directly to a color-coded spot,” said Steffen.
“Color 3D-printed protein models paint a more vibrant picture of an otherwise invisible molecular universe. Transparency and color coding are necessary features to create high quality, durable models.”
“Thanks to the J750, I will be able to
print multi-colored transparent scientific models while completely eliminating
a costly and time-consuming fabrication and assembly process. It’s a game
changer for me and my customers,” said Steffen.
Voytek partners with Shapeways to 3D print medical cable organizers

Most patients leave the hospital or a busy doctor’s office with a vision of medical equipment and cords and cables snaking everywhere. With an obvious need for better organization, Voytek Medical began working with Shapeways to 3D print products for locking in patient cables to protect medical equipment usually attached to monitors or roll stands.
Voytek was able to try out new products for their line, and
affordably so, allowing them to grow at their own pace and settle on the best
materials for the specific needs of their customers.
“Voytek Medical has been using Shapeways in every stage
of production, from concept to prototype and end-user products,” said the
Voytek team.
“In the trial-and-error phase of our designing, the use of extrusion desktop 3D printing in ABS was the best option available to us at the time. This material was far from precise, very brittle, and the layers tended to separate over time. From that point, stereolithography was used that brought us into the world of really designing with a purpose and good quality.”
Medical 3D printing requires advanced tools
If you look back
over the previous few decades, materials have not changed all that much, from
thermoplastics to metal. The ways in which they are used has changed immensely
though—whether in manufacturing 3D printed models or devices like prosthetics,
implants, or molds. 3D printing means combining advanced materials with
advanced technology for manufacturing high-performance parts at an accelerated
rate.

Shapeways offers over 10 different
technologies for manufacturing, and 90 different materials and finishes. Find out more about the materials and technology available at
Shapeways for 3D printing customized medical models, devices, and tools here. Upload up to 20 models at a time, receive instant quotes—and
look forward to consistent, quality drone parts that are durable and meant to
last in tough conditions.