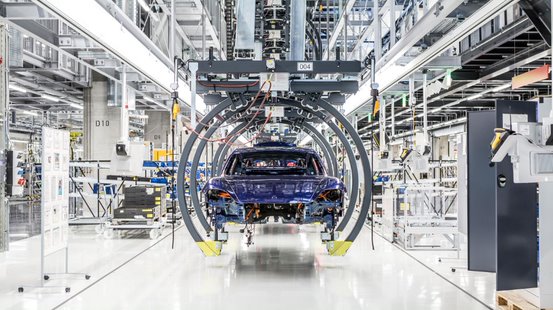
Thinking back to the beginning of 2020 can seem like a lifetime ago. Before the pandemic took root on a global level, the transportation industry was already in the midst of a great and exciting transition. The move to electric vehicles (EVs) was intensifying.
Take General Motors, for example. In early March, the company announced it would have 20 new EVs by 2023. It also is tackling ambitious innovations with its Ultium battery and propulsion system that could enable a GM-estimated range up to 400 miles or more on a full charge with 0 to 60 mile-per-hour acceleration as low as three seconds.
And then COVID-19 hit. Sales for all vehicles plummeted. But new consumer revelations were (and are) occurring on a daily basis — and it is good news for the EV market.
People are appreciating how skies can be clearer and bluer with fewer cars on the road. We’re learning the value of our time and resources with lessons in how to shop more efficiently with fewer trips. With a growing unease in taking public transportation, the demand for electric bikes and cars is also skyrocketing.
While governmental incentives for the EV market in the United States are minimal, the private sector is jumping on board to continue the momentum and meet the new consumer demand.
In June, Lyft announced that every vehicle on its platform will be electric by 2030. Despite a setback in the construction of its factory during the shutdown, Rivian will debut its electric pickup truck and electric SUV next summer. The company is also on track to manufacture more than 100,000 electric vans for Amazon. And GM isn’t shying away from its announcement and commitment to EVs, stating in May that it is continuing at full speed.
But there is still much more that needs to change and be done.
The present and future opportunities for EVs
What can be done to propel the EV industry even further despite the current global climate with COVID-19? Like anything in today’s landscape, it’s complicated — but it’s possible to achieve new inroads.
Let’s be honest. EV design and manufacturing comes with an entirely different set of challenges, even without a global pandemic as a backdrop. From EV design to manufacturing and battery optimization and production, we must address needed changes head-on for a radical, new approach to design and manufacturing.
Battery changes
Of course, not every company can be GM and create its own battery system. That’s why there is a need for greater openness in battery design and production — and what is actually inside the “black box” battery pack provided by manufacturers. If we can tap into the battery itself, we can further innovate for more efficiency.
Battery packs contain components such as cooling, sensors and battery management systems that, if more open, could allow engineers and designers to optimize storage and layout for energy efficiency. With the development of integrated digital design tools, the hope is that addressing both the battery and the car’s geometry in one combined design process will lead to greater efficiency for both.
Manufacturing changes
Even before COVID-19, automotive manufacturers and suppliers already were looking at new ways to modernize factories for better performance and reduced energy consumption.
Last fall, Porsche opened a new, innovative factory to manufacture its first fully electric sports car, the Taycan. The zero-impact facility is the largest built since the company was founded 70 years ago, and it is also one of the first in the world to begin use of driverless transport systems within the factory. It’s a great example of not only the acceleration of EV availability in the market, but a better way to approach manufacturing, too.
COVID-19 and its disruptive impacts on the global supply chain have accelerated how manufacturers and OEMs are looking at their production for more resilience. When factories shut down, it was a chance to step back and think of embedding sustainability throughout operations, in the factory layout itself, or leveraging more additive and local manufacturing. That also means greater opportunity to bring EV manufacturing and production more into the fold and mainstream.
EV design changes
On the vehicle design side, there are still untapped opportunities to improve battery range, especially through lightweighting and friction reduction. Frictions can be reduced by employing computational fluid dynamics software for simulation. And using generative design, designers can look at an incredible array of options to reduce the overall weight of the car.
Imagine taking an EV design and inputting the parameters to optimize such as geometry, materials, mechanical properties or even the manufacturing process. With generative design, the design team can explore the generated solutions and prioritize and choose what is most important for their goals. What’s more, the power of generative design truly shines when coupled with additive manufacturing to reduce waste in production. It even can solve some supply chain challenges for parts availability.
GM has been putting generative design to the test, especially for lightweighting. Its very first proof-of-concept project was for a small, yet important, component — the seat bracket where seat belts are fastened. With parameters based on required connection points, strength and mass, the software returned more than 150 valid design options. The team quickly identified the new seat bracket with a unique, unimaginable style, which is 40 percent lighter, 20 percent stronger and consolidates eight components into one 3D-printed part.
Driving forward
If 2020 has taught us anything, it’s that we are all much more resilient than we thought possible. This global pandemic is offering us an opportunity to reflect on a future we want — one that is not only more sustainable, but also more equitable for all.
We are embracing change as never before. As we all adapt to our new reality, industries also follow suit. Change and adaptability always has been endemic to the EV industry. We have made huge strides already. Now it’s time to keep driving forward.