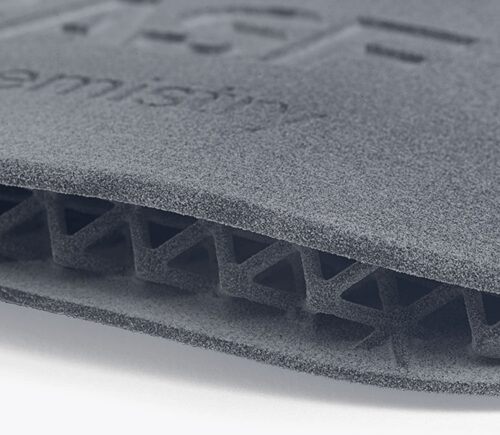
Created in a German lab in 1937, Thermoplastic Polyurethane (TPU) is now one of those ubiquitous plastic materials that spans numerous technologies in industrial manufacturing. Considering the appealing combination of thermoplastics and rubber for a variety of necessary applications, it’s easy to understand why TPU is so popular in 3D printing as well as other traditional types of manufacturing like injection molding. The versatility of TPU stems from the combination of hard and soft segments making up its block polymers, lending itself to the most common reasons manufacturers turn to 3D printing today: versatility and customization.
The Advantages—Where to Begin?
Shapeways offers TPU in off-white for use with Selective Laser Sintering (SLS), using EOS 3D printers, as well as Ultrasint TPU01 material from BASF, available in gray, using Multi Jet Fusion 3D printers. These materials offer multiple benefits over other elastomers, to include:
- Superior tensile strength – Defined by how much strain a part can take before fracturing, tensile strength is measured through units of pressure called megapascals (MPa). With a high tensile strength of up to 60 MPa, coupled with good flexibility, TPU can be used for high-performance parts that must stand up to rigorous use.
- Elongation at break – This material characteristic is tested by comparing where a part breaks after being strained, versus its original length. TPU is known for high elongation at break due to its elasticity, making it especially useful in critical applications because it is also so tough.
- Excellent load-bearing capacity – This is an important measurement as it testifies to how much weight a 3D printing material can handle—a factor that could be extremely important in applications requiring high-performance products that are expected to last, including mechanical devices like tubing, hoses, and seals.
- Resistance – TPU is able to stand up to many different factors because of its natural resistance, which is why it is considered such a multi-purpose 3D printing material. This includes resistance to chemicals, oil and grease, harsh weather, heat, and abrasion.

Typical Applications for Thermoplastic Polyurethane
Automotive
While the automotive industry has been using 3D printing for decades in prototyping, as well as functional parts for both the interiors and exteriors of vehicles, TPU allows for the design of components that focus on greater comfort for the driver, like customized headrests and seats. With TPU, textures may range from soft and luxurious, to rigid and functional, depending on the interior part for a vehicle. There are a variety of different finishes available too for automotive applications.
Consumer accessories
The 3D printing industry is well known for expanding options to consumers in the area of accessories, mainly due to the enormous potential offered by expanded design freedom and the ability to customize. This is especially true for items like smartphone cases, allowing customers to completely personalize an item, adding exciting and unique touches to an item that is pretty much impossible to live without. TPU is also an excellent choice for adding quality and customization to highly functional items used daily like rubber mats and products like handles.
Footwear
3D printing has made a powerful impact within the footwear industry, and on multiple levels. Designers working from their studios or homes are able to make creative new eco-friendly designs on demand and send them to Shapeways for 3D printing services. Large corporations are using materials like TPU to max out designs for epic, futuristic looking running shoes with a range of features meant to propel athletes and everyday wearers forward in terms of comfort and stamina.
There is also the potential for incredibly personalized fit in shoes, beginning with insoles that can be 3D printed to encourage better support and balanced gait, as well as orthotics that can be made to fit and re-sized easily as needed. With rapid production in 3D printing, more durable footwear products can be made that are also more flexible, and lighter in weight.
Medical devices
Another area where 3D printing is offering enormous impact, TPU is behind the production of numerous medical devices bearing complex, lightweight geometries that may not have been possible before with traditional manufacturing. Products like braces, prosthetics, and implants can be 3D printed, offering patients safe, customized devices that are able to stand up to long-term daily use without causing skin irritation.
Robotics
TPU is also suitable for robotics, and especially softer applications which may require extremely flexible parts like connectors, actuators, and simulated fingers, arms, and flex grippers for performing tasks whether on a manufacturing production line or at the individual level. This material can also be used for tires and other accessories attached to moving robots, as well as those that may be performing 3D printing activities on their own.

Sports gear
Because of the protective nature of sports gear, 3D printing technology with TPU is able to play a very important role in helping to prevent injuries in players. Using lattice structures for interior strength, 3D printed protective gear may include helmets, guards, and more, all with the potential to be heavily customized for the comfort and safety of the athlete.
Get Started with TPU Now
Upload your 3D models now to get started with printing in TPU using industrial SLS technology or in Ultrasint TPU01 using MJF technology.
